Typically used to augment the seal or holding force of a mechanically joined assembly, anaerobic adhesives are used as threadlockers, thread sealants, retaining materials and flange sealants. When designed into an assembly, these adhesives reduce component inventories, decrease total manufacturing costs, enhance equipment reliability, and minimize aftermarket breakdown and associated warrantee problems.
By definition, anaerobic adhesives remain liquid until isolated from oxygen in the presence of metal ions, such as iron or copper. For example, when an anaerobic adhesive is sealed between a nut and a bolt on a threaded assembly, it rapidly “cures” or hardens to form a tough cross-linked plastic with tenacious adhesion to many metals. Though anaerobic applications differ widely, in most cases the adhesive provides high shear strength.
-
When used to lock threaded assemblies together, anaerobic adhesives prevent loosening and corrosion of the fastener, maintain proper clamping force, and offer controlled torque for removal of the assembly.
-
For rigid cylindrical assemblies, such as joining a bearing onto a shaft, anaerobic adhesives known as retaining compounds enable manufacturers to bond parts that once could only be assembled using press fits or shrink fits.
-
Anaerobic gasketing materials are widely used as formed-in-place gaskets that produce leak-proof seals between mating flanges, preventing leakage of moisture, gasses, fluids or contaminants.
Anaerobic adhesives fixture in minutes at room temperature and fully cure within 24 hours. Full cure of anaerobic adhesives may be achieved more rapidly using short-term exposure to heat (e.g. 30 minutes at 120 degrees Celsius). In assemblies where a liquid primer or activator is required to accelerate cure, the primer is applied to one or both fastener surfaces before the adhesive is applied. No mixing of components is required.
As an anaerobic adhesive cures in a threadlocking application, it forms polymer chains that find their way into every tiny imperfection in the threads. Thread friction increases with the application of threadlockers due to interfacial connections to the surface roughness of the metal. The adhesive completely fills the microscopic gaps between interfacing threads to positively lock and seal threaded assemblies, preventing lateral movement and protecting the joint from corrosion that can result from moisture, gasses and fluids.
A typical nut-and-bolt assembly has as little as 15 percent metal-to-metal contact. Just a few drops of liquid threadlocker fills the remaining air voids between the thread roots and then cures to a thermoset plastic which provides a 100 percent unitized assembly until the user wants it to come apart. These adhesives offer high torque strength, good temperature resistance, rapid cure, easy dispensing and good vibration resistance.
Threadlockers are available in low-, medium- and high-strength formulations. Most threadlockers are color-coded for strength, with purple and blue representing low- and medium-strength grades, and green and red representing high-strength grades. However, no threadlockers are permanent; the low- and medium-strength grades can be disassembled with common hand tools at room temperature, and the high-strength threadlockers can be removed following direct exposure to 450-degree Fahrenheit temperatures.
The strength and viscosity of the adhesive needed for an application are directly related to the size of the fastener used. Low-strength threadlockers are used on screws up to one-fourth of an inch in diameter. Medium-strength materials are for fasteners up to three-fourths of an inch in diameter.
High-strength threadlockers are best used on fasteners up to one inch in diameter found in permanent assembly applications. Low-viscosity penetrating threadlocking formulations also are available that easily wick into pre-assembled fasteners up to one-half inch in diameter.
In applying threadlocking adhesives, the adhesive must wet the total length of the thread engagement area. Proper wetting is dependent on the size of the thread, the viscosity of the adhesive and the geometry of the parts. If the parts are large, then wetting both faces provides the necessary reliability for adequate adhesive application.
For through-hole nut-and-bolt assemblies, threadlocker should be applied only where the nut and bolt will meet when the assembly is fully tightened, as only adhesive between the threads will cure.
For blind-hole assemblies such as cap screws, threadlockers should be applied to both the bolt and into the bottom of the hole. If adhesive is applied only to the bolt, air pressure will force the liquid threadlocker to escape as the bolt is torqued down, resulting in an insufficient amount of threadlocker and possible assembly failure.
The greatest challenges faced with traditional anaerobic adhesives have been: 1) promoting cure on a wide range of metallic and non-metallic substrates that may be contaminated with grease or oil, 2) long-term exposure to elevated temperatures greater than 300 degrees F, and 3) long-term exposure to high levels of mechanical stress.
New surface-insensitive threadlocking formulations have been developed to be forgiving of oily and contaminated surfaces, curing in spite of residues that would inhibit cure of traditional threadlocking adhesives. In addition, these threadlockers also are designed to cure more easily on passive or inactive substrates such as plated or annodized surfaces, reducing applications where primers are needed.
While traditional threadlocking adhesives can withstand only limited temperatures (minus-65 to 300 degrees F), new anaerobic adhesives that incorporate innovative chemical technology have been formulated to maintain their integrity at temperatures up to 400 degrees F.
These products are ideal for applications that endure extreme thermal cycling, such as automotive and aerospace assemblies. New toughened formulations also have been developed to provide better overall performance under extreme thermal and mechanical stress. Because these materials are tougher than traditional anaerobics, they are less impact sensitive and can withstand prolonged exposure to intense vibration, rotational, shear and tensile forces.
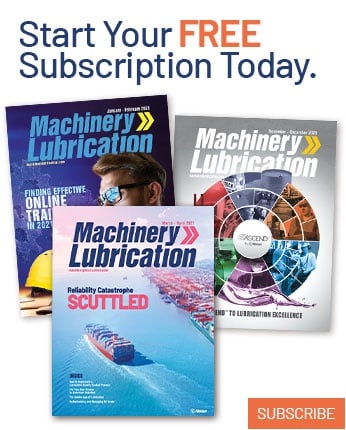