“It takes many people, doing things right, to keep the stacks smoking, morning through night. ... The hot strip, cold strip and the mills that run plate. Need the deliveries on time, can’t afford to be late. Keep those flatbeds rolling, get them out of the gate. ...
“‘Hey, the mill just went down, go find the trouble. Grab your tools, man, and work another double.’ Orange hats, yellow hats, white hats and more. Who cares about the color, get the steel out the door. ...
“The weekend is gone, let’s get back to the grind. You can work many jobs, but it’s tough to find ... a better group of people in this world, I feel, than the ones who are working to make American steel.”
Excerpt from the poem “The Steel Mill” by George Konig
It does take many people doing things right to keep an American steel mill up and running, and churning out product for the national market. However, in steel towns like Fairfield, Ala., an industrial burg located in the shadows of Birmingham, it’s become harder than ever to find them.
Fairfield was founded as a company town for workers of the Tennessee Coal, Iron and Railroad Company, which was purchased in 1907 by U.S. Steel. During World War II, U.S. Steel’s Fairfield Works employed more than 45,000 workers. Most adults in the town either worked at U.S. Steel or for a business that provided some level of support for the company and its workers.
Instructor James Hammonds (front left in white shirt) poses with students
at Fairfield Works’ maintenance training center.
Today, approximately 2,000 workers at the mill achieve record-setting production numbers. The site cranks out 2.4 million tons of raw steel each year, incorporating it into its sheet and seamless tubular products.
The demand for labor – the hard-to-find-’em conundrum – isn’t on the production side at Fairfield Works; automation and state-of-the-art manufacturing methods enable the mill to run lean. The shortage is in maintenance. In the past four years, the department has lost 25 percent of its workforce (from 600 workers in 2002 to 450 today), primarily through the retirement of highly skilled technicians (Baby Boomers who had 30 or more years of experience).
New maintenance employee Danny Davis
works on a shaft alignment project.
“The retirements came too quickly,” says Andrew Bissot, who joined the maintenance team in 2001. “Maintenance workers took advantage of retirement opportunities, and those tap-outs overwhelmed us.”
In the past, the mill addressed retirements by running help-wanted ads, and filled the ranks with highly skilled, fully qualified workers from the street. Today, that is nearly impossible because of:
-
Low unemployment: The Greater Birmingham area has an unemployment rate of less than 3 percent.
-
(Linked to No. 1) The emergence of the automotive industry: Mercedes, Hyundai, Honda and Toyota – and their suppliers – have shiny new plants in Alabama. “The competition is severe for the maintenance skills that are out there,” says Fairfield Works human resources manager Bernard Borman.
-
The general dearth of technically skilled young people: “Parents push their kids to go to college to become accountants and doctors, not maintenance employees,” says Borman. “They aren’t sending them to a trade school to learn a craft.”
-
Hurricane Katrina and the rebuilding of Louisiana and Mississippi: For the past year, companies in those states have offered large salaries and benefits to lure skilled workers to the Gulf Region.
This is a pressing issue, and it’s not going away. Bissot says the average maintenance workforce age in some Fairfield Works mills is in the “50-plus” range. “They can pretty much retire in the next 10 years,” he says. Because of the current and near-future situations, the site has stressed the need to hire approximately 200 new maintenance employees over the next five years.
Training center manager Andrew Bissot (center) makes
a point as students Mike Freeman (left) and Phillip Thomas
calibrate a proportional feedback valve.
Hot-rolled, cold-rolled and galvanized sheet products are
made for the metal building components, automotive
and appliance industries.
Impossible, you say? This steel plant survived the Great Depression – not to mention a couple of world wars and a host of other corporate, political, financial and social challenges. It simply got “back to the grind” and developed an innovative solution, a college-like maintenance training center to entice job candidates and craft the next generation of skilled technicians.
Maintaining the plant’s unique blend of
equipment is a challenge.
“We couldn’t find maintenance employees, so we had to do something different,” says Borman. “We had to select, train and develop our own.” In a little more than a year, the center went from a mere concept to a fully functioning education center that’s currently training 37 new maintenance employees. This is an idea that needed to work. As Konig stated frankly in his poem, steel has to get out the door.
Just the Facts
|
Site: U.S. Steel’s Fairfield Works, located in Fairfield, Ala., seven miles southwest of Birmingham. The site was established in the 1890s to be a steel and mining plant for the Tennessee Coal, Iron and Railroad Co. The site was purchased by U.S. Steel in 1907. Site size: approximately 1,200 acres. Plant employment: The site employs roughly 2,100 employees, including 450 in maintenance. Hourly workers are represented by the United Steelworkers union. Products: The plant makes sheet and tubular products; hot-rolled, cold-rolled and galvanized sheet products are made for the metal building components, automotive and appliance industries; the seamless pipe mill makes tubular products (4.5 to 9.875 inches OD) for the oil industry. Fairfield Works facilities include: blast furnace, three basic oxygen process furnaces, ladle metallurgy facility, twin slab caster, four-strand billet caster, hot strip mill, pickle line, six-stand cold reduction line, galvanize line, anneal and temper line, rotary piercing mill, stretch reducing mill, Austenitizing furnace, quench unit, temper furnace and sizing mill. |
THE NEED FOR AGGRESSION
As the talent pool of skilled and available maintenance workers began to dry up at the turn of the century, Fairfield Works took a close look at skills training and workforce development. Its former approaches in this area were to usher green maintenance technicians, or operators in search of a career path into maintenance, to local technical colleges or to the plant’s Institute for Career Development (ICD). There was also the option of informal on-the-job training (OJT). These options achieved varying degrees of success because:
-
Employees had to take classes on their own time. And since the plant was so busy and shorthanded, overtime took up that available time.
-
ICD painted training with a broad brush. “ICD wasn’t only teaching maintenance for electrical/mechanical people,” says Bissot. “They were also teaching guitar lessons, how to rebuild lawn mowers, how to lay down ceramic tile. They had real estate and motivational speaking classes.”
-
The ICD maintenance classes also were coming up short. “We didn’t do a good job of updating the curriculum,” says Bissot. “We weren’t training to Fairfield’s needs.”
-
Technical college training was general in nature. “We needed skills specific to the steel industry and to Fairfield Works,” says Borman.
-
Informal OJT can range from comprehensive to “a pat on the back, and off you go.” How do you know if standard, structured and safe “best” practices are being delivered? How do you know if the training is effective or not?
“We knew we had a labor shortage. We had to fill those positions inside the plant. We had to maintain the efficiencies and effectiveness of the mill,” says Bissot. “The only way to do that was to get more aggressive in our training.”
Progress toward a solution began in March 2005. The plant hired General Physics (GP), a consulting firm that helps companies optimize their technical and workforce performance. For the next several months, GP assessed Fairfield Works’ maintenance training practices, pointed out deficiencies and offered recommendations. The sides then worked together to create the concept of an internal maintenance training center that would develop skilled employees. The plant named Bissot, a 28-year-old maintenance shift manager from the cold reduction mill, as the maintenance training manager.
The training center would be housed in an 11,000-square-foot section of the 50-year-old Flintridge Building, the sprawling former headquarters for U.S. Steel’s Southern District. The complex is less than a mile from the plant.
CORE CONTENT
Development of the training program began in January 2006. Bissot and GP’s Don Langley etched out the curriculum for maintenance technician electrical (MTE) and maintenance technician mechanical (MTM) training sequences after completing a monthlong fact-finding mission.
Fairfield Works manufactures 2.4 million tons’ worth of sheet and
seamless tubular steel products each year.
“We went to every mill shack in the plant and interviewed the front-line maintenance employees,” says Bissot. “We wanted the opinions of the wrench-turners. We asked a ton of questions. ‘What training deficiencies do you have? What equipment at your mills requires additional training? What are the strengths and weaknesses of the way we’ve traditionally trained? What have you noticed about new employees coming in from the old curriculum? What was good and bad? What do we need to develop in these people.’”
The maintenance training center also provides
instruction for mill operators.
Bissot presented the planned curriculum to plant management, human resources and local United Steelworkers union leaders. With some minor tweaking, the educational framework was established.
The 33-module MTE sequence includes instruction on subjects such as industrial electricity, industrial electronics, process control and instrumentation, welding, hydraulics and pneumatics, AC drives, DC drives, fiber optics and vital control elements. The 30-module MTM sequence includes training on subjects such as clutches and brakes, couplings, chains and belts, shaft and coupling alignment, hydraulics, welding, drives, and AC and DC theory in crane controls. GP took the lead role in assembling the content for each module.
With content in place, the training model would work as follows: Candidates (current Fairfield Works operations employees as well as any non-U.S. Steel workers) apply to be a maintenance employee, and, consequently, a student in the program. Accepted applicants take a written test on technical subjects. Those that pass the test advance to take a stringent, 10-hour hands-on evaluation, called the Skills Performance Measurements. Those that pass are offered a job.
2007 will mark Fairfield Works’ 100th year as a U.S. Steel site.
The strengths and weaknesses of each new maintenance employee are assessed and a training program is developed for the individual. If a person is determined to have sufficient knowledge on a given training element (i.e. welding), he or she can bypass the class.
“If someone is already fluent on a particular subject, there’s no point to reteach it,” says Bissot.
A courseload of the remaining required sequence elements is then scheduled with the individual and the center.
Upon joining U.S. Steel, new maintenance employees then split their time between the training center and the plant floor. They, along with five to six fellow newcomers, take a two-week-long class. Approximately 30 percent of each course takes place in a classroom (the lessons come via textbooks, PowerPoint presentations and Q&A sessions with the class’ instructor, an experienced Fairfield Works maintenance employee). Focused sessions with the instructor in a laboratory comprise the other 70 percent. Written exams and hands-on projects are included during the two weeks.
After the two-week period, each “student” receives three homework assignments, called OJT (on-the-job) requisites. An OJT trainer (an experienced maintenance technician) is selected for each student. The trainer oversees requisite progress and performance and serves as a sounding board. Completed requisites are returned to the course instructor for approval and credit.
DEMOLITION AND DUMPSTER DIVING
In January, while the coursework and testing procedures were being developed, the center’s new home got a facelift.
“When we got here, this area had purple-painted walls and flowery wallpaper. The floors had 20-year-old carpeting and some asbestos tile,” says Bissot. “We knocked down walls, did the construction, did the abatement and ran the electrical.”
By the end of the month, the shell of the center looked great. In February and March, Bissot used some of his budget, plus a whole lot of creativity and persuasion, to fill the classrooms and laboratories with hands-on materials. (Specialty lab rooms were built for crane boards, process control equipment, electromechanical equipment, motors, drives, bearings and more.)
“We wanted to give them experience with and exposure to real-life equipment,” he says. “Some new equipment was purchased. But, we also used all of our resources. While we were at the mills doing the self-assessment, we were finding and getting our hands on non-utilized equipment and things we could use for cut-aways.”
There was a decent amount of dumpster diving. For example, a 2.5-inch back-pressure regulator was going to be scrapped at a cold mill. Bissot got the OK to scoop it up. He had it cut in half and painted to highlight the pressure-drop areas across the valves.
There was some wrangling. One mill had an excessive amount of belts sitting on a storeroom shelf. He persuaded the area to give him two belts and two spares for a soon-to-be-disposed air compressor.
E-mails went out. He messaged warehouse managers and workers in Fairfield and other U.S. Steel sites, looking for handouts. “I’d go, ‘Fellas, I’m looking for a conduit bender or a threading machine. Do you have any that you need to get rid of?’” he says. Plants sent surplus or non-used items.
Calls came in. The blast furnace upgraded the piston pumps in its hydraulic system. One phone call to Bissot and a short drive later, the old (still functional) pumps were being loaded into the back of his pickup truck. One is currently used as a rebuild trainer and another is used as a cut-away demonstrator.
The center was well-stocked as a result of these transactions.
“We were just a bunch of Legomaniacs,” he says. “It took outside-the-box thinking.”
The project was completed at approximately half of the original estimated cost.
“We had to report on every item that went from the plant to here. The reports fill a file folder that’s 3 inches thick,” he says.
Frugality was important since U.S. Steel was fully funding the project. While Birmingham and the state of Alabama offer funds to corporations for workforce training and development, monies are earmarked for companies in existence for 15 or fewer years.
INSTRUCTORS INSTALLED
With the curriculum and training center in place, all that remained were instructors and students.
In April, the center began accepting applications from bargaining unit employees for the five instructor positions. Why did U.S. Steel specifically seek hourly maintenance employees to be the teachers?
“They understand the plant and have the experience. They truly know the equipment associated with the plant,” says Borman.
Langley and GP vice president Chuck Kooistra had extensive interviews with the 21 applicants. The candidates then had to create a 15-minute teaching session and present it to a full classroom. Based on work knowledge and experience, the interviews and the ability to present information in an effective way, GP recommended five individuals for the teaching roles. Those selections were approved by plant management.
The center’s instructors and their focused training areas are:
- James Hammonds, automation
- Sidney Franklin, electrical
- Sam Gothard, mechanical and power transmission
- Jerry George, hydraulics and pneumatics
- David Dawson, welding
Hammonds is representative of the skills and experience found in the center’s instructors. A 28-year veteran at U.S. Steel, he has worked as an instrument, electronic and systems repairman, and as a foreman. In his spare time, he’s taught night classes at Bessemer Technical College, Lawson State Community College and RETS Electronics Institute, and coaches youth football.
“I enjoy training and teaching because everybody at some point has to be trained. A baby has to learn to walk and talk. If a kid is starting football, he has to learn how to block and tackle and run the ball. Training is essential to all of our lives,” says Hammonds, who is scheduled to teach math basics and classes on programmable logic controllers, process control, industrial electricity and industrial electronics.
The five instructors aren’t the only teachers at the center. At various times, guest instructors are brought in to share their wisdom. In a recent measurements and tools class, George invited Johnny Rutledge to be a guest instructor. Rutledge has worked at the plant since 1941.
“I’m teaching about safety and the mechanical side,” says the 83-year-old Rutledge, whose own training in the early 1940s consisted of job shadowing and being a “go-fer” for older workers. “This is a much better solution for training.”
Ray Widener, an electronics shop worker who Bissot calls “the guy in the plant when it comes to DC cranes and controls,” serves as a guest instructor on those subjects.
Says Bissot: “If we want our students to be the best, we might as well call on the best to share some of their vast knowledge.”
WINNING THEM OVER
The Fairfield Works maintenance training center, while impressive, would be worthless if there weren’t any students to teach. Remember Borman’s comment that “the competition is severe for the maintenance skills that are out there”? Could U.S. Steel win this battle for the minds and hearts of those examining the job market?
By offering a good wage and benefits package, and by promoting (internally and through a variety of media outlets) the fact that U.S. Steel has a training program that creates multi-skilled, in-demand industrial professionals, the number of job applications has been significant. For its initial search for program candidates in April, Fairfield Works received 140 applications. Those candidates came from the plant (operations workers) or through ads published in newspapers.
“They thought of themselves as being fully qualified for this position,” says Bissot.
THE CENTER ISN’T JUST FOR NEW EMPLOYEES
|
New maintenance employees aren’t the only ones using the Fairfield Works maintenance training center. During most weeks, you’ll find a group of 20 or so operators on hand for a three-day, eight-hours-per-day “operators performing maintenance” class. In the class, operators learn how to best assist maintenance workers through daily inspection and lubrication of their machines. The class curriculum is built around the CLAIR (Clean, Lubricate, Adjust, Inspect and Repair) principle. Over the next two years, the plan is for every Fairfield Works operator to complete the course. Andrew Bissot , the training center’s manager, says there is also the potential of exposing some operations leaders – manager associates and new managers – to the 24-hour class. Veteran maintenance employees also can use the center. “We have an intranet-based program coming out that will show available seats in curriculum classes,” says Bissot. “If a technician or manager feels the need to be trained in an area in which they are rusty or lacking, they can sign up for a spot.” |
Of the 140 applicants, 65 passed the written test, putting them at the talent equivalent of a Labor Grade 3 or 4 maintenance employee. Of the 65, a total of 46 received qualifying marks in the Skills Performance Measurements and were offered employment. Of the 46, a total of 37 candidates (26 Fairfield Works operators and 11 “off the street”) accepted the job. Nearly all were on hand when the training center had its grand opening and official start on June 5. The first classes were on lockout/tagout, rigging and scaffolding, and math basics.
Why would a Fairfield Works operator make the switch to maintenance?
“Maintenance is the better job,” says Mike Freeman, 33, who had been an operator in the pipe mill. “If something would happen here, you have the experience and skills to fall back on. Besides, before I came to U.S. Steel, I worked in maintenance at a water treatment plant. This is the field I wanted to get back into.”
Why would an outsider pick maintenance at U.S. Steel?
“The training here is top notch,” says Wade Murchison, 40, who was a pipe welder at chemical plants and refineries along the Gulf Coast before seeking employment at Fairfield Works. “I’ve been through training at a bunch of other companies, and it’s nothing like we have here at U.S. Steel. When we get through this training, it will be almost like having an associate degree. Plus, they aren’t training us to be specialists. They’re training us to be well-rounded technicians.”
“This program allows you to immediately implement classroom knowledge in hands-on mill work as you transition to and from the mill and classroom,” says Phillip Thomas, 38, who left a maintenance job at International Diesel in Huntsville, Ala., for the job at U.S. Steel. “This was a great move for me.”
Jim Bennett, the state of Alabama’s labor commissioner, summed up the positives at the center’s grand opening, stating, “U.S. Steel is making a significant investment in workforce development in Alabama and providing lifelong skills to members in our community who might not otherwise have access to this level of training.”
U.S. Steel is hot on the trail for the next groups of training center students (as stated earlier, Fairfield Works needs 200 new maintenance employees within the next five years). The company is expanding its efforts in Internet-based recruiting and has posted an application link on the U.S. Steel Web site. It has stepped up its listings in the region’s newspapers. ICD made adjustments to its maintenance curriculum in order to become a springboard program for current operators. And, the company’s public relations team has sent press releases about the center to a variety of media outlets, hoping for coverage and promotion.
“The unemployment rate in this area is very low, but we think we can get people interested in what we have to offer,” says Bissot. “There is a bunch of technically skilled people in Alabama. They may be working at a mom and pop transmission shop or changing oil at a Wal-Mart garage. There are people with technical certificates in auto mechanics. Those are the guys we want to tap on the shoulder and say, ‘Hey, take a look at this.’”
IMMEDIATE IMPACT
The training program has done more than just impact the size of the maintenance workforce. In its first few months, it made a positive impression on safety and plant reliability.
Students were adding fresh sets of eyes and incorporating a healthy “why do we do it that way?” attitude while completing OJT requisites. Troubleshooting projects brought solutions to sticking problems and updates to standard operating procedures. Homework projects were identifying potential safety issues before they evolved into safety problems.
On one OJT requisite assignment for the rigging and scaffolding class, new employees took inventory of shackles and cable slings in a storage area. Upon close inspection, they found a few shackles with worn threads and some slings with broken strands. As a result, the items in question were discarded and new ones purchased.
“We’re enforcing standardized practices; good, safe habits; and work that is going to enhance the reliability of the plant,” says Hammonds.
The students are also taking the center’s clean-and-neat environment to the mills.
“They’re learning that if they keep the equipment as clean on the floor as it is in the laboratory, it will be easier to troubleshoot,” says Bissot.
IT’S ALL GOOD
Momentum is high at Fairfield Works’ maintenance training center.
Bissot answers the center’s phone these days with a cheery “maintenance training center, the home of the professionals.”
Other manufacturing companies are calling the site, looking for tours and benchmarking opportunities.
By November, between eight and 10 of the first-group students will have completed their MTE or MTM curriculum.
“We are rebuilding the organization with these maintenance people,” says plant general manager Merle Stein. “It’s good for these new employees, good for the plant, good for U.S. Steel and good for the Fairfield community.”
POETRY IN MOTION
Fairfield Works is writing a new chapter in its nearly 100-year history. In deference to the poet Konig, it could read as follows:
“It takes experienced and new people, doing things right, to keep the stacks smoking, morning through night.
“The training center draws in smart new recruits. They learn and explore and get hands-on, to boot.
“With full brains and skilled hands, they’ll hit the plant floor. They’ll increase reliability and get the steel out the door.
“The job market’s tough, but fresh ideas have revealed ... the next wave of techs who help make American steel.”
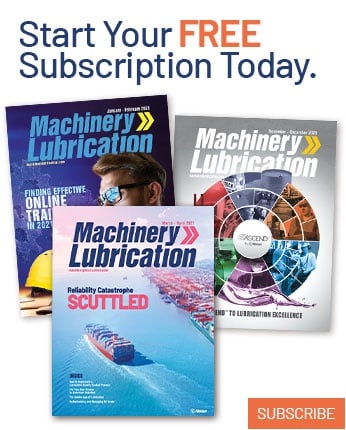