Infrared technology can detect subtle variations in motors, pumps, conveyors and other machine components. For decades, portable, infrared cameras have provided non-contact temperature measurement on a constantly expanding list of applications.
Infrared technology provides real-time analysis of entire “scenes” allowing for quick and safe monitoring. Infrared technology is an accepted and credited maintenance technology generally considered to offer the best return on investment of predictive maintenance tools.
The numbers of infrared cameras in the field have increased dramatically over the last 10 years. Technology improvements have opened the doors to potential infrared users who never considered infrared cameras in the past due to cost.
With an increasing base of infrared users and applications, the challenge is to leverage the technology effectively. Proper use of infrared technology requires an understanding of the components and the fundamentals of the technology.
Fundamentals of Infrared
Infrared energy is part of the electromagnetic spectrum and behaves similarly to visible light. It travels through space at the speed of light and can be reflected, refracted, absorbed and emitted.
Figure 1
Infrared radiation is a form of electromagnetic radiation, which is longer in wavelength than light. Other types of electromagnetic radiation are X-rays, ultraviolet rays and visible light. Infrared detectors or systems are categorized by their wavelength.
The unit of measurement is the micron. For example, a system that can “see” from 8 to 12 microns is considered a longwave, infrared camera because it “sees” in the longer side of the infrared spectrum.
All objects emit infrared energy as a function of their temperature. This means all objects emit infrared radiation. Infrared energy is generated by the vibration and rotation of atoms and molecules. The higher the temperature of an object, the more the motion and hence the more infrared energy emitted. The cameras do not see temperature, they detect thermal radiation.
Figure 2. Petronas Towers
E+T+R=1 – Kirchoff’s Law
No IR camera reads temperature directly. IR cameras read the IR energy coming from a target which includes: E emitted, T transmitted and R reflected energy.
As we discussed earlier, all targets emit energy. The infrared radiation that is emitted by a target is dependent on two things: the absolute temperature of a body and the emissivity of the body.
Emissivity is a material property. It is the efficiency of the body as a radiator or emitter. In our world, emissivity might be defined as the ability of an object to absorb infrared energy. We calculate emissivity as a property set by a number from 0 to 1. 0 would be a perfect R, or reflector – all energy that strikes the target with a 0 emissivity would bounce off of it. Any object with an emissivity of 1 would be a perfect absorber – all energy that strikes the target with a 1 emissivity would be absorbed. Neither example exists in nature.
It is important to note the emissivity is not a set number. It is a material surface property and is affected by shape, viewing angle, wavelength and temperature.
Reflectivity,in our case, is infrared energy that bounces off our target. Reflectivity defines the energy on a target that was not emitted by the target itself. Often defined as Tref or Tamb in cameras, it is the temperature of incident radiation from the target’s surroundings.
Transmissivity of a material is the percentage of infrared radiation that transmitted through it. For example, glass has poor transmissivity in the longwave, infrared spectrum. Thus, infrared camera manufacturers often use Germanium for their lenses. Germanium has almost perfect transmissivity in the longwave, infrared spectrum. When dealing with infrared systems, spec sheets, salespeople, users, etc., will often only address the issue of emissivity. However, emissivity is only one-third of the equation.
If we are interested in temperature measurement, we must realize only the sum of an object’s emittance, transmittance and reflectivity will get us to the complete number 1 and, for our work here, an accurate temperature measurement.Remember, E+T+R =1 gives us our best chance for accuracy.
Spot size ratio
Another important factor when considering measurement is spot size ratio. Spot size ratio is the ability of an infrared camera to measure an object from a given distance. Infrared systems have to average a certain number of pixels together to calculate an actual temperature. For example:
Figure 3.
The cross hair, or Spot 1, in the above image has a circle in the middle. The circle represents the number of pixels that are averaged together to create a temperature reading. Any object we want to measure has to “fit” inside this circle. If our target does not completely fill the circle, we know we will be finding average surrounding components, and, thus, temperatures around our target.
Spot size is usually represented as a ratio. For example, an infrared system with an approx. 20’:1” spot size ratio can measure a 1-inch object from 20 feet away. Remember, a spot size ratio is a ratio. As we move closer or further away from the target are spot size ratio will grow correspondingly smaller or larger.
Pixel count and optics play a large part in determining the spot size ratio of an infrared system. For example, if we assume the same optics for three systems with different pixel counts, 160x120, 320x240, and 640x480, we will have significantly different spot size ratios. The larger the pixel count, the smaller or more densely packaged the pixels on the detector. The more pixels we can get on a smaller target, the better our spot size ratio.
For example, below are three images saved by three different systems. The images were taken from the same distance with approximately the same optic configuration:
Figure 4.
Figure 5.
Figure 6.
Notice the maximum temperature in scene results:
160x120 Infrared System – 127 degrees F
320x240 Infrared System – 243 degrees F
640x480 Infrared System – 280 degrees F
As our spot size ratio increased, we are measuring a smaller and smaller point and, thus, measuring a more accurate hot spot. In fact, we can actually see an impending problem on the 640x480 image that we could not see in the other images.
A telephoto optic improves the spot size ratio of an infrared camera by narrowing the field of view. By tightening the pixels into a narrower field of view, we can place more pixels on a target and improve our accuracy.
For example, a spot size ratio of a 160x120 infrared system with a standard, 25 degree lens is approximately 10’:1”. If we use a telephoto, 12-degree lens in place of the 25-degree lens, our spot size ratio improves to 20’:1” despite the fact we are using the exact same camera.
However, by using a narrow field of lens, we have doubled the amount of area we have to scan. An argument for higher resolution cameras is that we can often use standard lenses with wider field of views and still measure small components from distances.
Common mistake: Over-emphasizing Temperature Measurement
Ever since the introduction of radiometric systems there has been a tendency to rely on temperature measurements as an indicator of component operability. NETA and others have generated “equipment severity ratings” based on temperature.
Therefore, through training and subsequent research, infrared thermographers have become accustomed to providing temperature measurements in their reports. However, a large issue for “temperature measurement” is whether that measurement is meaningful or not.
For example, let us consider a relatively small, apparent, Delta T between two battery studs. In our example, the temperature of the bad stud is 119 F, +/- 3F. Under most common severity guidelines, this would be classified as a minor problem.
The important information regarding this component is not necessarily the temperature but the electric current (load) running through it. The battery stud is hot due to high resistance. At the time of measurement, the battery was being trickle charged 60 milliamps (MA). The battery was rated for 200 amps.
Ignoring the fact that the resistance and heat transfer will increase with temperature, a simple ration of the power dissipated at a load of 200 amps, the connection would dissipate about 11 million times the power it is in the images. This would cause a failure that we would have missed! The load (current) is one example of a crucial factor in electrical system analyses.
Common mistake: Ignoring temperature measurement
Since we have just discussed relying too much on temperature information, we should consider the inverse. What if we only relied on qualitative finding?
For example, measurement of a hot conductor indicates a hot spot at the connection. Common methodology would indicate that the corrective action is to clean and tighten the connection. This may solve the connection problem but is the connection problem the whole story.
Measurement tells us in this example that the conductor temperature is 115 degrees Celsius, at or above the temperature limit on the cable insulation. The insulation has degraded to the point where new conductors must be pulled to correct the problem.
Quantitative thermography is essential when equipment temperature limits are approached. There are many other examples where quantitative measurements are required such as diagnosing steam traps, safety relief valves or determining corrective action priority.
Common mistake: Misidentification of components
The many hats that infrared thermographers have to wear include the hat that says “expert.” Whether you like it or not, you are considered the expert in whatever you are looking at with your IR camera. It is very tough for a non-electrical person to identify electrical components. There is no excuse for not correctly identifying components yet this is done every day.
Sources for the correct identification of components include plant personnel such as mechanics, electricians, technicians as well as engineers, management, equipment operation manuals and the industry groups on the Internet.
Conclusion
IR is an extremely useful predictive maintenance tool. By learning more about infrared properties and how infrared cameras operate, we can learn how to more effectively apply the technology.
References
- Excerpts from “Fundamentals of IR,” InfraredTrainingCentercourse manual
- Excerpts from “Don’t let the RAT bite you,” Mikael Croholm, ITC International, from InfraMation Conference
- Excerpts from “How to Guarantee Your Failure as an Infrared Thermographer,” Ron Lucier, ITC instructor, from InfraMation Conference
- Excerpts from “A Primer on Infrared Thermography V2.” Gary L. Orlove and Robert P. Madding, ITC instructors
- Excerpts from “Emissivity Measurement and Temperature Correction Accuracy Considerations,” Robert P. Madding, ITC instructor
About the author:
Travis Curtis is a sales manager for FLIR Systems Inc. For more information, visit the FLIR Web site at www.flir.com.
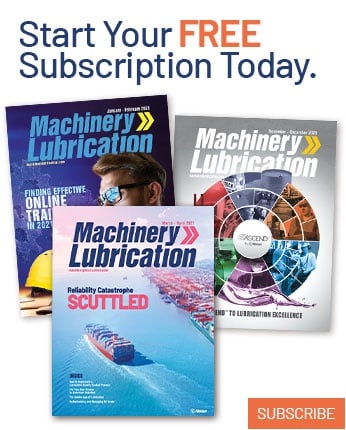