Managing a multi-technology condition monitoring program at a large mining operation was a challenging task, especially when there has been a cultural shift required to integrate the ideas of condition monitoring into an already complex maintenance strategy.
One of the major challenges included shifting the focus of an experienced maintenance crew from a run-to-failure mentality to a proactive mentality.
Another major challenge was folding the new work practices into the current work flow model, one which didn’t have a lot of emphasis on backlogged maintenance items.
Finally, coaching the supervision and management about why this is the right move proved to be one of the more difficult tasks of all.
But now less than a year later, dramatic results are being realized. As the condition monitoring statistics trend in the right direction, maintenance costs are shifting sharply as well.
Overtime has dropped, and unplanned downtime has decreased significantly. The best part is the workforce is becoming more and more focused on fixing problems rather than fixing machines.
Multi-Technology Condition Monitoring Case Study
The Four Corners Mine is a large, open-pit mining operation located 25 miles south of Lakeland, Fla. Four Corners is one of six mines belonging to The Mosaic Corporation, the world’s 13th-largest producer of phosphate fertilizer. The Four Corners Mine produces approximately 6.5 million tons of phosphate rock annually. The mine has three distinct areas:
-
Dragline Operations: Electric draglines are used for mineral extraction. There are six draglines averaging 50 cubic yards each.
-
Field Pumping System: 82 large 2,000-horsepower pumps are used to move the unprocessed phosphate rock (matrix) from the draglines to the float plant. This makes for nearly 70 miles of 20-inch and 22-inch pipe.
-
Float Plant: The float plant includes numerous conveyors, vibrating screens, pumps and log washers that are all used to clean the phosphate rock and separate the debris and unwanted material.
All told there are 775 pieces of rotating equipment on the entire facility. There are 270 employees at the
Four Corners Mine, with 110 of them in the maintenance department.
The Four Corners Mine embarked on the implementation of a multi-technology condition monitoring program in March and has seen some very dramatic changes take place since then.
Understand the Challenges
There were and still remain several large challenges to getting the process completely ironed out. Like any process that involves more than one person, the relationships between the people play a vital role in continued success.
Each of the individuals has to develop a level of trust in the others and as a group they have to develop a unified sense of purpose. Finding and retaining qualified personnel is another large challenge.
Condition monitoring personnel who want to work in a mining environment and have any experience at all are very difficult to come by. As everyone begins to work together on a daily basis attitudes and personalities start to play major roles in the group’s effectiveness and efficiency. Keeping all these technical people working and working together can prove to be a daunting task.
One of the key challenges is developing an understanding of the process between the maintenance group and condition monitoring group. The maintenance people have to understand the condition monitoring process, and the condition monitoring people have to understand the maintenance process.
Without each fully grasping the other’s process and where they themselves fit into the other process, any kind of forward momentum will be difficult to initiate.
Finally, internal group politics can play a large role in extinguishing improvements in the overall process. If there are individuals who tend to not give credit where credit is due, hard feelings can develop. On the other hand, if the leaders of the change process are quick to hand out pats on the back and do it often, then everyone feels they are appreciated and tend to work even harder to advance the cause.
Desire to Succeed
Another key role in the success of any process is a strong desire to succeed. That desire is easily seen at the Four Corners Mine. The maintenance manager is the catalyst that keeps the program rolling on a daily basis. The manager’s attitude toward condition monitoring as a part of the overall maintenance strategy is what keeps the rest of the maintenance department focused.
Above the maintenance manager, in the corporate office, the desire for the program to succeed is seen as well. The benefits of the condition monitoring program have been folded into the overall financial strategy of the mining operations at the Mosaic operations of central Florida. The condition monitoring program is expected to produce results in the safety, costs and availability areas of the overall plan.
The safety measures have been affected by means of reduced overtime and call-out work. When crafts personnel are not called out as much at night to work on equipment that has failed during a scheduled production shift, the likelihood for injury has been reduced.
When the precise nature of a problem has been identified prior to work commencing and the craftsmen don’t have to spend unnecessary time and effort looking for the problem, the likelihood for injury has been reduced.
Being able to identify problems and get them corrected long before additional damage happens to other components of a machine reduces the overall cost of the repair. All of these add up to reduced unplanned downtime which is increased machinery availability.
Figure 1. Technology vs. Asset Ranking Graph.
Multi-technology Program
The Four Corners Mine decided early to employ as many condition monitoring technologies as they could to provide the highest likelihood of identifying the actual failure modes of the assets.
Vibration analysis, contact ultrasonic emissions, oil analysis and mechanical infrared thermography were chosen to identify rotating machinery defects. Motor circuit analysis and electrical infrared thermography were chosen to identify the failure modes of the electric motors and the associated switchgear. See Figure 1 for the percentage of coverage by technology.
Best Technology Available
The Mosaic Company also decided early on that an investment in the best technology available would help ensure the best results. CSI 2130s were chosen as the vibration analysis platform. Mikron infrared cameras were chosen for the thermography effort. The UE Systems 10,000 was selected for contact and airborne ultrasonic analysis. And, the venerable PdMA MCE/Emax was selected as the motor circuit analyzer of choice.
Figure 2. Integrated Condition Status Report
Web-based Reporting
A Web-based reporting platform is used to communicate the results of all condition monitoring technologies to Mosaic personnel. A Web-based reporting tool was selected for numerous reasons:
-
It requires no software to be installed on customer’s computers.
-
It can be accessed from any computer with access to the World Wide Web.
-
It is not limited to any particular hardware or software platform for the different technologies.
-
It is easily expandable as other technologies are added or removed.
Mosaic wants all levels of supervision to be involved in the identification and elimination of machinery faults. Consequently everyone has access to the software. Figure 2 shows an example of a report available in the software that summarizes all of the problems identified in a given area of the plant.
Integrated Work Flow
A fully integrated work flow model would be defined as one where both the Mosaic personnel and the Allied Reliability personnel had equal ownership in getting the work identified and accomplished. Figure 3 shows the work flow model, which is color-coded to quickly identify who is responsible for which part of the process. It was decided that this integrated workflow would provide the following benefits:
-
Get Mosaic and Allied interacting on a daily basis.
-
Ensure Mosaic personnel took ownership of certain portions of the process.
-
Technician can make clear recommendations not just alert the customer to the technical aspects of the problem.
-
Interaction at the lowest level creates a learning process for both the technician and the craftsmen.
-
The “Post Check” is the feedback loop for the maintenance repair process.
Relationship between the technician, supervisor and mechanic … crucial for success.
Figure 3. Four Corners – Condition Monitoring Work Flow Model
Workforce Education
It was agreed that workforce education was an important foundational element that would keep the process going. Four Corners continues to make a significant effort to educate all maintenance employees about P-F intervals (see Figure 4). In addition, technology familiarization was also a major topic.
Making all of the front-line supervisors and craftsmen aware of the different condition monitoring technologies and how they worked was seen as a key component of gaining acceptance. The reliability engineers conduct monthly “lunch and learn” sessions where sandwiches are brought in and key program elements and/or technology demonstrations are discussed.
Figure 4. P-F Interval
Dedicated Focus
Without a dedicated focus, it is very easy to lose sight of the goal. To ensure this didn’t happen, Four Corners dedicated a good portion of the reliability engineer’s time to overseeing the process.
Their goal is to maintain maintenance engagement and awareness while at the same time measuring and benchmarking the maintenance department’s results and success as well as Allied Reliability’s. Successes are purposely celebrated at weekly meetings and misses are clearly identified and root causes eliminated.
Figure 5. MTBF – Motor Failures (2005)
Constant Improvement
The entire process must be inundated with an attitude of constant improvement, and at Four Corners, it is. The maintenance manager is always pushing for more and better results. The reliability engineers are always pushing for more detailed explanations of problems and more focus on eliminating root causes. In an effort to help maintain this focus, Allied Reliability provides Four Corners with a monthly report on numerous measurements.
-
Percent of Red, Yellow and Green Condition Entries, both overall and by technology
-
Percent of Condition Entries Implemented
-
Number of Work Orders Generated
-
Route Compliance
-
Average Time to Implementation
Real-world Measures
What follows are three graphs representing the effect that Four Corners’ attitude toward constant improvement and condition monitoring has had since March 2005.
Figure 6. Emergency Work Order (2005)
Figure 7. Field Pump Bearing Assembly Usage
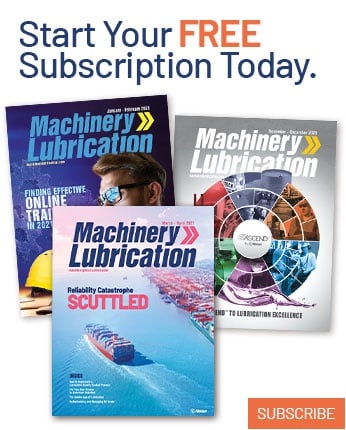