Bearings on a large induced draft fan in the boiler system at a major hardwood mill in the Northwest were failing in as little as four to six weeks of operation. Bearing life was extended dramatically by replacing the existing split-block SAF-type double-row roller bearing pillow blocks with Rexnord ZAF6000 Series SHŪRLOK Adapter Mounted Roller Bearings. It also simplified a time-consuming installation procedure.
At the mill, alder, maple and other hardwoods are processed into dimensional lumber. A boiler that provides heat for the kiln burns dust from the planer/sander. After combustion, the induced draft fan removes any unburned dust as well as the ash and moves it to the bag house. The fan, approximately 30 inches in diameter, turns on a 2-7/16” diameter shaft that is supported by two bearings. Driven by a 50-horsepower electric motor through a 1.5:1 speed increaser V-belt drive, the fan runs at 2,648 rpm.
Environmental conditions including heat, dust and an overhung load contributed to the short life of the previous bearings. In addition, their split housing made it necessary to assemble the bearings and set clearances on site. The installation method for the split-housing bearings requires pre-measuring the clearance and then tightening the tapered adapter nut in increments, using feeler gauges to determine when a specified reduction in clearance is reached. If this procedure is performed correctly, the shaft grip force will be correct, but it is often performed incorrectly. If the shaft grip is too loose, the bearing may loosen on the shaft. If it is too tight, the clearance in the bearing is reduced, which can generate excessive heat. In addition, the dust and ash particles in the air made it almost impossible to keep the bearings clean during the assembly and installation procedure.
Bearings on this induced draft fan at a major hardwood mill were failing frequently before they were changed to Rexnord ZAF6000 Series SHŪRLOK Adapter Mounted Roller Bearings.
Easier Installation also Helps Extend Bearing Life
To extend bearing life and reduce installation time, the company replaced them with ZAF6000 series SHŪRLOK bearings that are solid-housed, shaft-ready units and are a drop-in to the traditional SAF units. They are greased and the clearance is preset, so they can be taken out of the box and mounted immediately to the shaft, which eliminates contamination and clearance uncertainties. They feature a positive locking system that maintains mounting tightness during operation. The tapered adapter sleeve provides greater shaft grip and eliminates the shaft damage caused by loose bearings. In addition, the tapered sleeve makes it easier to remove the bearings from the shaft without causing damage, saving both time and repair costs. The new bearings also incorporate Spyglass Optical Strain Sensors (OSS), which provide instant feedback to achieve optimal shaft grip. They eliminate damage to the shaft and bearing caused by improper tightening during bearing installation.
Closeup shows new bearings in place, with induced draft fan housing at right and guard for V-belt speed increaser at left.
Two slightly different types of bearing were used in this application. While a ZAF 6207 was installed on the drive side, a ZAFS6207 was used on the fan side. The latter bearing is a floating unit that allows the cartridge that holds the bearing to slide back and forth in the cast iron pillow block housing. This permits the bearing to accommodate shaft expansion caused by heat that may be present at higher speeds.
Shaft between V-belt drive and fan is supported by two bearings.
A company spokesman reports that it generally took at least three to four hours to replace the previous bearings. Typically, the new bearings can be installed in seven to 10 minutes each. He says, “We had to assemble the old bearings and check the clearance, but with these, we just slide them in place and the sight glass shows when we have the right tension. Because they are pre-packed with grease, we don’t have to guess there either.”
Previous split-block ball bearing design required field assembly that made it difficult to set clearances accurately and allowed contaminants to enter the bearing.
The spokesman points out that a bearing failure can be expensive for the company in more ways than just the downtime and repair costs. The boiler burns 14 to 16 cubic feet of sawdust a day, but if the blower is down, the company may have to contract to have the sawdust hauled away if the silo in which it is stored is full. While the previous bearings failed regularly in four to six weeks or less, the new bearings have been in service for more than six months to date, so the savings have been significant. This success may lead to exporting the solution to other company facilities, he concludes.
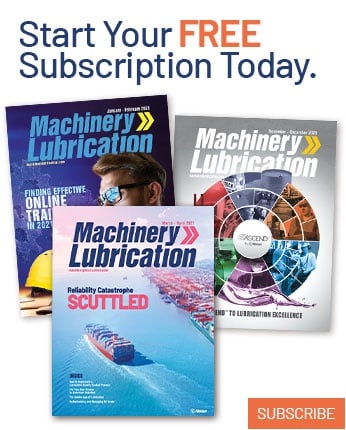