Now that maintenance managers and reliability engineers are being inundated with information on condition-based maintenance, one question that I frequently hear is, “Where do I start?”
Despite what you may have heard, the foundation of a successful program is a list – a detailed, accurate equipment list.
The reality is that your equipment list, or asset catalog, is a central data source for most of the key steps that follow. It contains the vital information you need to design, develop and engineer your program from the ground up.
Without a good list, you can’t:
-
identify the failure modes for your equipment;
-
choose the appropriate predictive maintenance (PdM) technologies to apply to each asset;
-
determine the right level of PdM coverage for your plant;
-
rank the criticality of equipment;
-
build databases for each PdM technology;
-
determine PdM staffing levels
Clearly, if your list is incomplete or inaccurate, the quality of these decisions will be questionable. So, any shortcuts at this stage can turn into big problems.
What makes a good list? For starters, it should include:
-
the equipment number;
-
a description of the equipment;
-
the equipment type (dryer, blower, motor, pump, etc.);
-
the equipment’s area and location;
-
the layout of the equipment hierarchy;
-
full make/model/manufacturer information
In essence, having access to good technical and engineering information helps take the guesswork out of maintenance decisions.
For example, in the case of vibration analysis, there is a catalog of virtually every bearing make and model. That means you can overlay the fault frequencies for a potential bearing fault on your data and verify if the frequencies for the bearings align with the data. But if you don’t know what bearings you have, you can’t do that. Then, it’s a matter of thinking you have a bearing problem as opposed to knowing you have one.
Surprisingly, most plants don’t have good asset records, unless the data was captured when the plant was built. If you don’t have this information, or if it’s less than 75 percent accurate, there are two options:
1) The manual approach: The conventional method is to examine each piece of equipment with clipboard in hand and write down the key data. The information is then transcribed into a database.
Depending on your plant size and the number of assets, it can be extremely time-consuming to physically walk around and gather information from the nameplate, go into the engineering files, find original OEM drawings and equipment manuals, and capture as much of that information as possible.
That’s why companies like Allied have developed another option:
2) Software tools: When time is a factor, equipment lists can be created much faster and easier with a tablet PC and a software tool. Here’s how it works.
First, your current equipment data is imported into a database. Then, as more information is gathered in the field, it’s entered directly into the database. After that, it’s simply a matter of exporting the compiled data to the appropriate PdM technology databases. This speeds up the process tremendously and greatly reduces effort compared to the manual, paper-based approach.
If you start with the correct list of the engineering specifications you need, one plant exam gives you all the data necessary to set up databases for each PdM technology. Otherwise, you’ll have to examine the plant multiple times for each technology. You can either work hard or work smart, but you will still have to work.
Ideally, you’d have all this information up front. But that rarely, if ever, happens. Sometimes, collecting good engineering data is a matter of timing. For example, you might have to wait until the plate is taken off a gearbox and then literally count the gear teeth.
However you decide to do it, don’t be tempted into shortcutting this step. A good list is one of the most overlooked and underappreciated keys to success in condition-based maintenance.
The bottom line is this: Having accurate asset records will help you make better decisions on maintenance, reliability and work management.
John Schultz is a partner with Allied Reliability and a Certified Maintenance and Reliability Professional through SMRP. As the largest consulting, engineering and service firm focused on predictive and preventive maintenance, Allied Reliability serves more than 200 plants and facilities in the U.S., Canada, Europe and Latin America. For more of John’s insights, get a free copy of “PdM Secrets Revealed! How to Improve Your PdM Program or Start One from Scratch” at www.alliedreliability.com. For answers to your specific questions, call John at 812-841-9252 or e-mail him at schultzj@ alliedreliability.com.
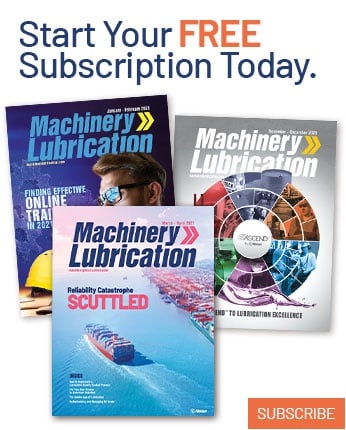