In June 2004, Canandaigua Wine Company (CWC) completed an upgrade project on the compressed air system at its winery in Lodi, Calif. Before the project, the winery depended on two compressors to satisfy its production requirements. Anticipating an expansion of its production capacity, the winery commissioned a review of the compressed air system by a U.S. Department of Energy Qualified AIRMaster+ Specialist at Atlas Copco Compressors Inc. This review prompted a system-level improvement project that enabled the winery to employ its existing compressors more efficiently and to add a more efficient compressor than the company had originally planned.
Plant/Project Background
Established in 1945, CWC markets and sells 20 brands of wines and beverages. In March 2004, CWC became part of a new organization, Constellation Wines U.S., which is part of Constellation Brands. Within the new organization, CWC operates as an independent sales and marketing company. Before the project began, the Lodi facility was served by two 125-horsepower rotary screw compressors. Because an expansion of 6 million gallons per year (a 40 percent increase in output) was being planned, the existing compressed air system would have been unable to support the additional load.
In a system audit, load patterns showed that the greatest amount of air that the process required was during the three-month fall crush season. The existing compressors had to operate at full load during this season to support production. However, during the rest of the year, both units were operated at partial load, wasting energy.
The project to improve the compressed air system’s efficiency included a proactive leak repair campaign, additional storage and a new controls package. Because the existing compressed air capacity was greater than the capacity needed during the nine-month off-crush period, plant personnel decided to implement a recommendation to install a 75-horsepower variable-speed compressor. This new compressor is versatile enough to satisfy plant demand during periods of low use, and it can also effectively supplement the two 125-hp compressors to provide enough air to satisfy plant demand during the crush season.
Results
The compressed air system project at CWC’s Lodi winery is yielding impressive results. Energy savings of 218,000 kilowatt-hours (kWh) and energy cost savings of $22,000 are projected annually, based on AIRMaster+ estimates and measurements of the system’s energy use. Because fewer compressors now have to operate at any one time, compressor run times have decreased. This decrease is projected to result in annual maintenance cost savings of approximately $5,000. Factoring in a $22,000 rebate from Pacific Gas & Electric, the company’s electric utility, total project costs were $33,000. With total projected annual cost savings of $27,000, the project will yield a simple payback of slightly more than 1.2 years.
Lessons Learned
When an industrial facility is retooled or about to undergo a production increase, its compressed air system should be re-evaluated to determine whether the system is configured efficiently and whether additional compressors are necessary. Had the CWC plant simply added a fixed-speed 75-hp compressor, the system would have been less efficient because the new unit would have used a less-efficient control strategy. Instead, plant personnel decided to install a variable-speed compressor that can adjust its output more closely to the system’s demand. The choice of this compressor was inspired by a system-level evaluation that provided the plant with a comprehensive strategy to improve the system’s efficiency. This resulted in significant annual savings for energy and maintenance while effectively supporting the production increase. Such an approach can be applied in a wide variety of industrial facilities that use compressed air.
Partner Profile
Mark Kiser, a sales/systems engineer with Atlas Copco Compressors, is an AIRMaster+ Qualified Specialist who has evaluated compressed air systems for more than 10 years. Kiser’s use of AIRMaster+ was instrumental in analyzing Canandaigua Wines’ compressed air system data and validating the results of the project.
Qualified Specialists are industry professionals who identify cost-cutting and efficiency opportunities in industrial plants. Experienced professionals who complete a qualification training workshop and exam for specific DOE-developed software tools receive special designations, and can use these tools to help plants reduce costs, decrease maintenance and downtime, and improve productivity. The training recognizes and enhances a professional’s expertise in the use of DOE’s AIRMaster+ software tool, Pumping System Assessment Tool, Process Heating Assessment and Survey Tool, and Steam System Tools. For information, visit the software tools Web page.
Benefits
- Saves $27,000 annually in energy and maintenance costs
- Reduces annual energy consumption by 218,000 kWh
- Reduces maintenance requirements
- Achieves a 1.2-year simple payback
Read More Energy Matters Articles on These Topics
This article was written for the U.S. Department of Energy’s Industrial Technologies Program and appeared in the DOE’s Energy Matters newsletter. For more information, visit http://www1.eere.energy.gov/industry/.
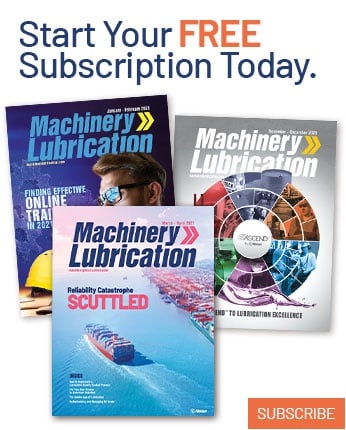