Businesses today are challenged to find more efficient ways to operate. Energy costs are rising and present significant long-term implications for the viability of many companies. Decision making, when it comes to the total cost of ownership, needs more focus than ever before. Designing for sustainability requires that you heed the thinking of Stephen Covey and “begin with the end in mind.” To reduce costs associated with energy consumption and waste generation, companies must maximize their investment using life cycle asset management methodologies.
Life Cycle Asset Management (LCAM) is the basis for making sound decisions from conceptual design through the disposal of any asset type, and is measured based on the long-term impact on your business. It examines the shortest time to market for a capital improvement project while delivering the lowest total cost of ownership in order to maximize returns. LCAM is a holistic approach that should be deployed within your company’s Front End Loading (FEL) engineering process.
LCAM data (including energy consumption) must be identified early in the capital investment process. The data and resources captured in the front end should be used to evaluate Life Cycle Costs (LCC) from cradle to grave in order to minimize the total cost of ownership. Adopting this approach to a capital project helps drive sustainability.
A Real-World Example
While working with a large pharmaceutical company, I was conducting a workshop on the benefits of designing for reliability when one participant spoke up, saying “Here is a good example of what not to do.”
This company needed a new visitors center to replace an older, less functional, less flashy building at their plant entrance. The new building was expected to make a statement about the company, and would house historical items and awards that the company was extremely proud to showcase. An architectural firm was hired to create design alternatives that were progressive in nature and illustrated the values of the company. One particular value to be incorporated was sustainability.
The building was constructed using glass as the exterior feature, and inside were modern and upscale materials reflecting the company’s leadership position in industry. Designing with sustainability in mind, the architectural firm incorporated energy-saving HVAC technologies specifically engineered and sized for the space, taking into account the inside dimensions of the building (A), the heat-loss coefficient (U) of the window materials, inside and outside temperature variance (To – Ti) and the number of degree days per year. An example of the calculation used to determine annual energy requirements for the prescribed technologies, expressed in Btu/hour, is:
Ht = AU (Ti – To)
Designs were finalized and the plans were contracted for the construction phase. During this phase, the procurement process began. The construction company went to their supplier base and approached this purchase with their departmental goal as the primary driver: “purchase at the lowest cost.” The procurement group was routinely rewarded for this type of performance, and worked to bring the glass in at the lowest cost, yet slightly outside of the original specification. This is where a significant issue compromised the future sustainability, LCC and energy efficiency of the building.
The construction project moved forward and the building was completed on time and under budget. I underline under budget to prove a point. How an organization measures performance can yield poor results and long-term implications. In this situation, the pharmaceutical site very quickly started experiencing issues with condensation, moisture damage and HVAC performance. Why was this happening? A site investigation confirmed that procurement practices, which purchased glass outside of the original design specifications, were the root cause of the problem. The replacement glass had a higher U-factor – energy coefficient rating relative to heat loss – and lower condensation resistance factor. The additional thermal load, caused by the variance in glass specification, meant that the originally specified and installed HVAC system was now undersized. At this point, much of the future was cast. The site would be stuck with the additional life cycle costs in order to maintain sufficient comfort levels within the building and prevent moisture damage due to inadequate dehumidification.
Calculating Energy-based Life Cycle Costs
Beginning with the end in mind, energy consumption expectations should be defined in any capital project that requires the installation of new assets or replacement of existing assets. Relative to the example described in this article, energy consumption of HVAC systems should be compared to the size of the space to be heated, cooled and dehumidified, the heat-loss coefficient of the materials used to construct the space, and the heat generation properties of the space (e.g. processing equipment, people and computers).
Let’s assume that the aforementioned pharmaceutical company was constructing a 5,000-square-foot visitor’s center, and that the originally specified window material had a U-factor (heat-loss) of 0.35, which is at the lower end of the spectrum derived by the American Society of Heating, Refrigeration and Air-Conditioning Engineers (ASHRAE). To calculate the estimated energy consumption rate per year, we must also determine the average outside and inside temperature differential. In this example, we will assume that the outside design temperature for the region is 27 degrees Fahrenheit, and the expected inside temperature is 70 degrees F. Using the equation Ht = AU (Ti – To), the HVAC system must maintain 75,250 Btu/hour in order to heat and dehumidify the space.
Ht = (5000 x 0.35) X (70 – 27)
Now, we need to determine the energy-based life cycle cost of the HVAC system in the space. Using the HVAC sizing rule of thumb to start our analysis, one ton (12,000 Btu) per every 800 square feet, we can determine that we will need a 6-7 ton unit for the 5000 SF visitors center using the originally specified window materials. For the sake of this example, we are going assume that the cost of electricity is $19 per million Btu’s (British Thermal Units). The cost of heating, natural gas, fossil fuels and electricity is circumstantial based on the fluctuations in market price by region, but $19 is a fair market value for the United Sates. We need one more data point and we’re ready to calculate energy cost, which is degree days – the number of days per year when heating is required. To calculate the degree days, subtract the outside temperature from the desired inside temperature. If the value is less than or equal to zero, that day has zero degree days. But if the value is positive, the resulting number represents the number of degree days. In many regions of the world, heating (or cooling) degree days are predetermined for engineering design purposes, so we’ll use 8,000 degree days per year for this example.
Multiplying 75,250 Btu/hour by 24 (one day), then multiplying that result by the number of degree days per year (8,000), we can estimate the energy consumption rate to be 14.4 billion Btu per year. At $19 per mBtu, the specified HVAC system sized for the specified construction materials will cost the pharmaceutical company approximately $275,000 per year.
If we further use this life cycle costing model to evaluate decisions throughout the construction of the building, we can ascertain the financial impact that the replacement glass had on sustainability. The most significant difference between the originally specified glass and those purchased as an alternative is heat-loss coefficient (U-factor). The replacement glass had a U-factor of 0.54, 55 percent higher than that of the original glass. When it comes to heat loss, the lower number is always better. If you supplement our calculations above using the new U-factor figure, we realize that this decision ultimately costs the pharmaceutical company just over $150,000 more a year in additional energy. If we evaluate this impact over a 10-year life cycle period for the HVAC system, this equates to more than $1.5 million of wasted expense.
How could this have been avoided? Simply answered, by following a clearly defined LCAM process that establishes “toll-gates” in order to evaluate life cycle cost as a result of decisions made throughout the construction of the building. Here are some steps towards sustainability to follow when beginning your FEL or capital engineering process:
-
Define the sustainability characteristics of the project, including overall energy consumption rate and maximum allowable waste generation.
-
Determine the sustainability cost categories that must be considered within the life cycle cost analysis (e.g. cost per million Btus)
-
Select for review only those design alternatives that support the sustainability characteristics.
-
Select the lowest total cost of ownership design for project execution.
-
Establish toll gates prior to each functional transition within the process. For example, before procurement hands the project over to construction planning they should again perform the life cycle cost analysis to validate that their material selections have not increased the cost of ownership over the predefined life cycle period.
About the author:
Bruce Wesner brings more than 24 years of maintenance, engineering and management experience to his role as managing principal for Life Cycle Engineering (LCE). His senior management experience with world-class companies includes work in a number of industries: HVAC (OEM Products), heavy steel fabrication (Tier 1 supplier), tubular steel fabrication (high-volume OEM production), high tolerance machining, pharmaceuticals and building products. Bruce’s strength is driving improvements through lean and reliability-based initiatives. Bruce can be reached at bwesner@LCE.com. For more information about Life Cycle Engineering, visit www.LCE.com or call 843-744-7110.
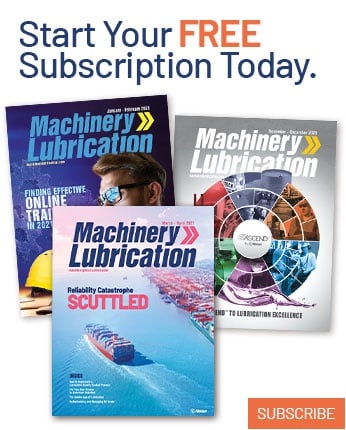