Lockout/tagout is a specific set of procedures to safeguard employees from unexpected energization or startup of machinery and equipment or the release of hazardous energy during service or maintenance activities.

What Is Lockout/Tagout?
The Occupational Safety and Health Administration (OSHA) defines lockout/tagout (LOTO) as a specific set of practices and procedures to safeguard employees from unexpected energization or startup of machinery and equipment, or the release of hazardous energy during service or maintenance activities.
Failure to control hazardous energy (lockout/tagout) consistently ranks on OSHA's top 10 most frequently cited standards. The lockout/tagout practices were put into place to prevent physical harm or death during the servicing and maintaining of machinery or equipment that isn't properly controlled. OSHA estimates complying with a lockout/tagout procedure prevents around 120 fatalities and 50,000 injuries each year, and that exposure to hazardous energy causes an average of 24 lost workdays for each injured employee.
An effective lockout/tagout practice requires a designated employee turn off and disconnect any machinery or equipment from its energy source(s) before doing any required maintenance on the asset. This authorized employee(s) should either lock or tag the energy-isolating device(s), preventing the unwanted release of hazardous energy. Additionally, the employee(s) should take additional measures to ensure the energy has been isolated effectively.

Lockout devices are designed to keep energy-isolating devices in a safe or "off" position, preventing machines or equipment from becoming energized. These devices can't be removed without a key or other verified unlocking mechanism or through extraordinary force by using bolt cutters or a similar tool. Tagout devices are warning tags attached to energy-isolating devices to warn employees not to turn on or re-energize the machine. Tagout devices are easier to remove and provide less protection. It's best practice to use the two together.
Types of Hazardous Energy Lockout/Tagout Protects Against
When people think of energy, they're most likely thinking about electricity. While electrical energy has the capability of being extremely dangerous, a lockout/tagout procedure aims to prevent injury or death from multiple types of hazardous energy.
- Lockout/tagout for electrical energy: When establishing a lockout/tagout procedure for electrical energy, consider all potential sources. Most machines get electrical energy through some type of circuit breaker. A lockout device can be placed on the circuit breaker to prevent electrical energy from flowing to the machine.
- Lockout/tagout for mechanical energy: Often overlooked when considering a lockout/tagout program, mechanical energy is created through the motion of an object. If an employee is performing maintenance on a machine and accidentally bumps a moveable part, it could pick up enough momentum and become dangerous. It's a good idea to put a lockout/tagout device on things like robotic arms, moveable saw blades, crushing parts or anything that can move unexpectedly.
- Lockout/tagout for hydraulic energy: Hydraulic energy is very common in manufacturing thanks to its effectiveness with heavy machinery. Lockout/tagout devices should be used with hydraulic equipment to prevent pressurized hydraulic oil from being released while someone is working on the asset. Sometimes hydraulic oil is pressurized with electrical brakes, which will disengage when the power is shut off. Part of the lockout/tagout procedure for hydraulics is checking to ensure energy has been released before work on the machine begins.
- Lockout/tagout for pneumatic energy: Similar to hydraulic energy, pneumatic energy is formed using pressurized air instead of fluid. If a machine or piece of equipment uses stored pneumatic energy, part of the lockout/tagout procedure is to release the built-up pressure before maintenance begins.
- Lockout/tagout for chemical energy: Chemical reactions can release energy, whether by mixing two or more chemicals together, altering a chemical's temperature, or a sudden change in pressure, among other factors. Burning gasoline in an internal combustion engine is one of the most common types of chemical energy. Lockout/tagout procedures for chemical energy might involve removing and locking out a diesel generator that serves as a backup power source.
- Lockout/tagout for thermal energy: Thanks to modern machinery, thermal energy is rarely encountered today, but it's a good idea to be aware of it. Thermal energy is energy gained from a heat source.
Keys to an OSHA-Compliant Lockout/Tagout Program
OSHA's Control of Hazardous Energy Regulation standard (29 CFR 1910.147) requires that, "The employee shall establish a(n) energy control program consisting of energy control procedures, employee training and periodic inspections to ensure that before any employee performs any servicing or maintenance on a machine or equipment where the unexpected energizing, startup or release of stored energy could occur and cause injury, the machine or equipment shall be isolated from the energy source and rendered inoperative."
- Define procedures: Establishing and standardizing energy-control procedures is step one. These procedures should clearly layout steps for removing the energy supply from machines and putting lockout/tagout devices on the energy-isolating devices (preventing re-energization). The established procedure must also address how to handle stored or re-accumulated energy.
- Outline a training program: Clearly outline and train employees on the energy-control program, including safe application, how to use lockout/tagout devices and the removal of energy controls.
- Audit: Periodically inspect the standardized lockout/tagout procedures (annually at minimum) to confirm that steps are being followed properly and that they are still effective in preventing employee exposure to hazardous energy.

There are six key elements you can follow to ensure your lockout/tagout procedure is OSHA compliant.
- Develop and standardize a lockout/tagout program: The development of a lockout/tagout procedure must be a collaborative effort from all levels. Documenting your lockout/tagout program for equipment energy control is vital, as it explains and details the elements of your program for all employees. Not only should you adhere to OSHA's guidelines, but you should also consider custom requirements requested by employees to help them understand the program and apply it on any given workday. Remember, the lockout/tagout program isn't set in stone and should be audited regularly to ensure it is relevant and effective.
- Write out machine- and task-specific lockout/tagout procedures: Lockout/tagout procedures should clearly identify the equipment in question. They should detail each specific step necessary for shutting down, isolating and securing equipment to control hazardous energy. Additionally, procedures should include steps for the placement, removal and transfer of lockout/tagout devices. Using visuals is a good idea to drive home each step. Machine-specific photos that identify each energy-isolation point can be placed at each point of use.
- Identify and mark energy-isolation points: Working from the equipment-specific procedures outlined in the previous step, find and identify all energy-control points with standardized labels and/or tags. Look for things like valves, switches, breakers and plugs.
- Lockout/tagout training and audits: Once procedures are standardized and energy-isolation points are labeled, it's time to train employees on how the lockout/tagout procedure works. Be sure to provide training on not only the OSHA guidelines but also machine-specific procedures as well. OSHA looks for a few things when evaluating a company's lockout/tagout training program:
- Who is the authorized employee(s)? This is the person or people who perform the lockout procedures on machinery.
- Who are the affected employees? These people don't perform the lockout/tagout requirements but use the machinery.
- Other employees. Any other employees who don't use the machinery but are working in the area near machinery that is being serviced.
- Place the proper lockout/tagout devices: A variety of lockout/tagout devices are on the market, all for different applications. From circuit-breaker lockouts and valve lockouts to multiple types of handle lockouts, it's important to obtain the proper device for each asset. After you select the appropriate device, document it and specify where it's being used. Other lockout/tagout devices you'll typically find include:
- Electrical equipment lockouts
- Cable lockouts
- Valve and hose lockouts
- Lockout hasps
- Labeled padlocks
- Battery lockouts
- Sustain: Post single-point lessons containing lockout/tagout procedures on equipment where devices should be placed. As mentioned earlier, your lockout/tagout procedure should be a document that is continuously improved. This means regularly scheduled audits should be done to ensure the procedures remain effective. Reviewing your lockout/tagout program consistently prevents you from having to start from scratch each year.
Developing a Lockout/Tagout Procedure
When it comes to developing a lockout/tagout procedure, OSHA outlines what a typical lockout procedure looks like in the 1910.147 App A standard. For instances when the energy-isolating device can't be located, tagout devices may be used as long as the employer complies with the stipulation that additional training and more rigorous inspections are needed.
The following steps in the lockout/tagout procedure lay the groundwork for the lockout of energy-isolating devices when servicing machinery or providing maintenance, according to OSHA standard 1910.147 App A. These steps should be used to verify that the machinery is stopped, isolated from all hazardous energy sources and locked out before any employee begins maintenance or servicing, preventing the machine from starting up unexpectedly.
When the lockout/tagout procedure is completed, it should detail the scope, rules, purpose, authorization and techniques employees will use to control hazardous energy sources and how compliance will be enforced. Employees should be able to read through the procedure and at least see:
- Instructions for how to use the procedures;
- Specific procedural steps to shut down, isolate, block and secure machines;
- Specific steps outlining safe placement, removal and transfer of lockout/tagout devices, as well as who is responsible for the devices;
- Specific requirements for testing machines to test the effectiveness of the lockout/tagout devices.
Lockout sequence

- Notify all affected employees. When it's time for servicing or maintenance, notify all employees that the machine needs to be shut down and locked out before performing the maintenance or servicing tasks. Record all affected employees' names and job titles.
- Understand the machine's energy source(s). The authorized employee(s) assigned for the lockout/tagout procedure should check the company procedure to identify the type and magnitude of the energy source the machine uses. These individuals must understand the potential energy hazards and know how to control the energy. OSHA clearly states the procedure must explain exactly what employees must know and do to control hazardous energy effectively.
- Shut down the machine. If the machine is currently operating, shut it down using the normal stopping procedure; push the stop button, close the valve, open the switch, etc.
- De-activate energy-isolating devices, so the machine is separated from its energy source(s).
- Lockout the energy-isolating device(s) using individually assigned locks or predetermined lockout devices.
- Dissipate stored energy. Stored or residual energy, such as that found in capacitors, springs, rotating flywheels and hydraulic systems, must be dissipated or restrained. This can be done via methods like grounding, blocking, bleeding down, repositioning, etc.
- Disconnect the machine from the energy source. This is done by first checking to make certain that no one is exposed and then verifying the machine is isolated from the energy source by going through the startup process of the machine, ensuring it does not start. If the machine remains off, it is not considered locked out.
The only exception to this standard is very limited. "If an employer can demonstrate the existence of each of the eight elements listed in 1910.147(c)(4)(i), the employer is not required to document the energy control procedure," according to OSHA standard 1910. This exception is terminated if circumstances change and any of the elements no longer exist.
After you've completed servicing or maintaining the equipment and it's ready to be returned to normal operating status, OSHA standard 1910.147 App A requires the following steps be taken:
Restoring equipment to service
- Walk around the machine, checking that all components are operationally intact and that only the essential items remain.
- Verify that all employees are in a safe spot away from the area.
- Ensure all controls are in the neutral position.
- Remove the lockout devices and startup the machine.
- You now can notify the affected employees that maintenance is complete and the machine is operational again.
Lockout/Tagout Device Requirements
Whether you use lockout or tagout devices, they should be provided by the employer and serve as the only energy-isolating devices used to control hazardous energy. OSHA outlines the requirements for lockout/tagout devices, as summarized below:

- The devices must be durable enough to hold up in workplace conditions. This means that tagout devices must not deteriorate and become illegible, even in wet or corrosive environments.
- The devices must be standardized according to shape, size and color. Additionally, tagout devices should be standardized regarding the print and format, and be understandable to all employees. Tagout devices must warn employees of the hazards that can occur if the machine is energized and offer clear instructions such as, "Do not start" or "Do not open."
- The devices should be substantial so they can't be accidentally removed. Other than using a key, devices should only be able to be removed using excessive force or with special tools like bolt cutters. Tags must be one-use, self-locking and non-releasable with a minimum unlocking strength of 50 pounds. Tags should be attached by hand using a one-piece nylon cable tie.
- The devices must be labeled to identify the specific employee(s) authorized to place or remove them.
Lockout/Tagout FAQs
Are there any scenarios where lockout/tagout does not apply to service and maintenance activities per standard 1910?
Per OSHA standard 1910, lockout/tagout does not apply to general industry service and maintenance activities in the following situations:
- Hazardous energy is controlled completely by unplugging the machine from an electrical outlet as long as the employee(s) controlling the machine has complete control over the plug. Additionally, this only applies if electricity is the only form of hazardous energy to which the employee is exposed. This includes things like hand tools and some cord-connected machinery.
- Hot-tap operations are performed on pressurized pipelines that distribute gas, steam, water or petroleum products. This applies if the employer shows that continuity of service is essential, shutting down the system is impractical, and the employee follows documented procedures and uses the necessary equipment for protection.
- Minor tool changes or servicing is being performed. This includes routine and repetitive services integral to production that occur during normal production operations.
How can I determine if an energy-isolating device can be locked out?
According to OSHA, an energy-isolating device can be considered capable of being locked out if it meets one or more of the following criteria:
- It's designed with a hasp or other part to which you can attach a lock, like an electric disconnect switch;
- It has a built-in locking mechanism; or
- It can be locked without dismantling, rebuilding or replacing the energy-isolating device or permanently altering its energy-control capability. Examples of this include a lockable valve cover or circuit-breaker blockout.
I can't lockout a machine. What do I do?
There are times when locking out a machine's energy-isolating device is not possible. If you find this is the case, securely attach a tagout device as closely and safely as possible to the energy-isolating device. Make sure it's immediately obvious to anyone attempting to operate the machine. Additionally, employees must be trained to be aware of the limitations of tagout devices, as they do not provide the physical restraint of lockout devices.
What if I use outside contractors for service and maintenance tasks?
In this case, both the outside contractor and the employer must inform each other of their respective lockout/tagout procedures. The employer must ensure that employees fully understand the contractor's energy-control program.
What if a shift changes during machine service or maintenance?
This is another instance when standardization is important. A standardized lockout/tagout procedure ensures continuity and should include instructions on the orderly transfer of a lockout/tagout device between incoming and outgoing shifts. If a lockout or tagout device remains on an energy-isolating device from a previous shift, the incoming shift employees must verify that the machine is, in fact, isolated and de-energized.
How often should I audit my lockout/tagout procedure?
Employees are required to review their procedures at least once a year. If it's determined that the procedure is no longer providing adequate protection, employers must make adjustments. Inspectors should review each authorized employee's responsibilities within the energy-control procedure. If tagout devices are used, inspectors should extend their review to affected employees due to the increased importance of their role in avoiding the accidental activation of machinery.
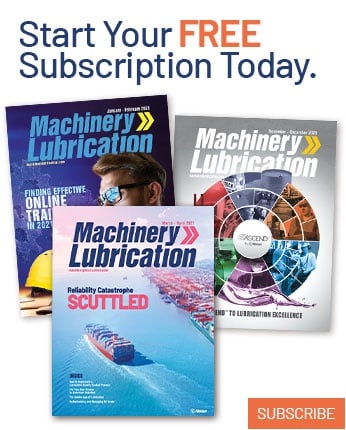