A Reliable Plant reader, a maintenance planner at a major U.S. utility, recently submitted this case study about pump vibration monitoring. It offers invaluable information to all of you who work on pumps.
During monthly pump vibration monitoring data collection rounds, a power station’s 500-horsepower vertical turbine circulating water pump experienced a large increase in vibration compared to the previous month readings.
The running speed vibration trend showed the November reading went from a normal 0.257 inches/second velocity to 0.468 inches/second in February, and then increased again to 0.637 inches/second in March. Analyst review of the data found the largest response at the top of the motor, which is normal for most vertical pumps as they tend to pivot at the pump discharge head mounting to the floor.
Resonance is common with this design of pump, however, the natural frequency of this pump/motor system was found to be well above the 500 rpm operating speed of the pump through the use of a simple bump test. The waveform pattern showing a predominant 1x (running speed) cycle supported an imbalance/wear condition.
Knowing this, shaft displacement readings were taken in an effort to judge the severity of the problem. After using a strobe light on the exposed pump shaft below the coupling to ensure no keyway or protrusion would interfere, a shaft stick (fish tail) with the pump vibration monitoring sensor mounted on it was safely held against the shaft. In the past, the shaft displacement had generally been around three to five mils. Now the vibration exceeded 16 mils, all at running speed.
Change of Plans Due to Pump Vibration Monitoring
A spring outage was previously planned in three weeks for this unit. Due to the rapid change in pump vibration and the severity, recommendations were made to pull the pump during this outage. The pump was monitored on a bi-weekly basis until the outage to ensure it would not catastrophically fail.
Preparations were made for impeller replacement as this was likely the source of the high running speed vibration due to imbalance, possibly from a broken vane due to foreign object damage or excessive wear ring clearances. This type of damage was suspected because this pump is in a pit fed by a nearby river and has a history of damage due to debris.
River water is screened into the intake house, however, during the spring, high river levels tend to bypass debris and repetitive failures of the screen wash system have allowed debris past the screens which travels to the pit at the plant.
However, plant management still needed convincing that this was the problem, so prior to the outage, divers were brought in to inspect the circulating water pit for debris and to look at the pump impeller. The pit was surprisingly clean, but the diver found the pump impeller tips damaged and an obvious offset to the fit of the impeller to the bowl. This likely meant that the impeller wear ring was worn excessively and/or the lower shaft was bent.
Scheduled for Repair
Armed with this information, the pump was then scheduled for repair during the outage. Upon inspection, the impeller wear ring was found worn, blade/vane tips were damaged/bent and the shaft was bent. Parts were available for repair, but additional time was required to order a new shaft.
The condenser was found with excessive debris, so the hypothesis is that the pump had passed large debris that likely bent the shaft. Repairs were completed within the timeframe of the scheduled outage and the pump was successfully returned to service.
After the outage, an inspection of the remotely located river water intake house found damaged intake screens and inefficient screen washing. In an effort to prevent any future failures to the circulating water pumps, repairs were made to the screen and a new screen wash pump with a stand-by unit were installed.
A new control system was added to sense differential pressure on the screen improving the overall efficiency of this system. Regular preventive maintenance inspections of the intake house system were developed and scheduled in the computerized maintenance management system to ensure this often neglected system is kept in good condition.
To date, less debris has been found in the condenser water boxes and the circulating water pumps have been running fine because of pump vibration monitoring, but we are still fighting the high water levels during the spring rains.
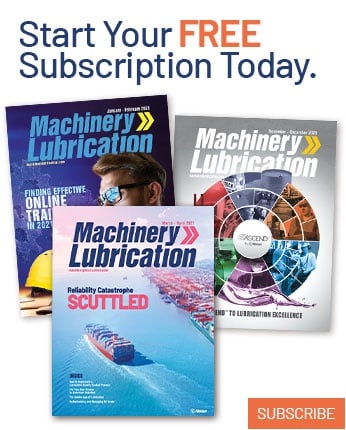