Emerson Process Management’s Smart Wireless technology is helping to provide valuable condition monitoring information at the Total Petrochemicals plant in Carling Saint Avold, France. The introduction of wireless transmitters provides new temperature measurement data, enabling the company to calculate changes over time in wall thickness on a boiler that provides steam to a steam cracker, enabling personnel to anticipate when it may need replacement.
By installing a wireless solution to connect the additional measurement points, Total Petrochemicals removed the need to install around 1 kilometer of new wiring. An additional benefit of the solution has been the reduction of movement of personnel into and around the at-risk areas.
Total Petrochemicals, part of the TOTAL group, is the fifth-largest petrochemical company in the world and produces a range of basic petrochemicals at the Carling site including ethylene, propylene, methane and styrene, as well as plastic consumer products including polyethylene and polystyrene. These products are produced by the process of steam cracking, whereby petroleum, along with either gas oil or naphtha, are mixed in a cracking oven with superheated steam at a temperature of 800 degrees Celsius.
Total Petrochemicals wanted to better understand the condition of the boiler and anticipate when it might need to be replaced. To achieve this aim, the company was keen to introduce a number of new temperature measurement points. By measuring the internal and external temperature of the boiler walls and identifying heat loss, it is possible to calculate the material’s resistance and infer its thickness.
“Our plant is more than 30 years old,” said Jerome Uszes, electricity control and regulation maintenance manager, Total Petrochemicals. “With the rising cost of copper and aging existing wiring (corrosion, infiltration, armature degradation, etc.), finding alternative methods to carry data throughout the plant is becoming essential. We believe in wireless technologies.”
This non-critical monitoring of the boiler walls presented Total Petrochemicals with the perfect opportunity to evaluate Emerson’s Smart Wireless technology on a large scale and in a real industrial environment. The application would also enable the company to determine the current limits of the wireless devices and to direct future developments made by Emerson’s research and development department.
Eight Rosemount 648 wireless temperature transmitters were installed directly onto the exterior of a boiler drum situated 50 meters above the ground. An Emerson Smart Wireless Gateway was positioned on the roof of a technical building around 300 meters from the devices. Two additional temperature gauges were installed in strategic areas between the boiler and the gateway to provide sufficient coverage to the area and to enable supplementary measuring points to be added in the future as required.
Data from the wireless transmitters is passed from the Gateway to a third-party DCS system via Modbus. From the control room, the operators have gained visibility of the thermal status of the boiler walls, allowing them to determine how the internal (process) and external (climatic) conditions impact on the material’s deterioration.
An additional wireless device, a Rosemount 3051S pressure transmitter, is providing redundancy for an existing wired device that provides a critical measurement in the plant. This transmitter also reinforces the wireless mesh and provides an additional path back to the gateway.
The Smart Wireless’ self-organizing mesh technology is very reliable, and each measurement point has a redundant communication via two or three routes. With Emerson’s self-organizing technology, each wireless device can act as a router for other nearby devices, passing messages along until they reach their destination. If there is an obstruction, transmissions are simply re-routed along the network until a clear path to the Smart Wireless Gateway is found. As conditions change or new obstacles are encountered in a plant – such as temporary scaffolding, new equipment or a parked construction trailer – these wireless networks simply reorganize and find a way to get their signals through.
All of this happens automatically, without any involvement by the user, providing redundant communication paths and better reliability than direct, line-of-sight communications between individual devices and a receiver. This self-organizing technology optimizes data reliability while minimizing power consumption. It also reduces the effort and infrastructure necessary to set up a successful wireless network.
“We eagerly await the availability of open standard WirelessHART™ products that guarantee interoperability. Once these are available, we can look to use Emerson’s wireless technology for control applications in the plant,” said Jean-Michel Glad, control and regulation reliability engineer, Total Petrochemicals.
About Emerson Process Management
Emerson Process Management (www.emersonprocess.com), an Emerson business, helps businesses automate their production, processing and distribution in the chemical, oil and gas, refining, pulp and paper, power, water and wastewater treatment, mining and metals, food and beverage, pharmaceutical and other industries. The company combines products and technology with industry-specific engineering, consulting, project management and maintenance services. Its brands include PlantWeb, Fisher, Rosemount, Micro Motion, Daniel, DeltaV, Ovation and AMS Suite.
About Emerson
Emerson, based in St. Louis, brings technology and engineering together to create innovative solutions for customers through its network power, process management, industrial automation, climate technologies, and appliance and tools businesses.
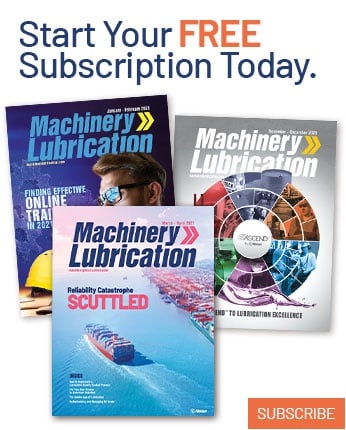