I can't help but draw parallels between how some families and plants function. I think the different departments in plants often interact with each other similar to that of families.
If departments are like family members, which department is the wife and which is the husband? Perhaps I'm out in the blue with this article, but to me it is clear as day. Operations is the wife and maintenance is the husband. Let me explain.
Think about who operates your family and makes the decisions? Lying husbands will say that they make the decisions; honest ones will admit that their wife does.
As an unavoidable consequence of this, it seems many husbands (and maintenance departments) end up with a "honey-do" job list. This is a list of work that your spouse (operations) feels must get done in the near future. My advice is for families (and plants) to be very careful how jobs actually end up on the list and how they are prioritized. The first step is to ask if the job really needs to be done. This question will enable families and plants to control their budget. If the answer to all job requests is "yes", the budget will be hard to control.
Discuss each item on the list as a joint partnership between husband (maintenance) and wife (operations). I suggest one of the first steps is to divide jobs into "necessary maintenance work" and "improvements". Improvement work is rarely as important as repairs. The work that makes the list then should be prioritized. This simply means agreeing to when the work will be completed at the latest.
(A warning note for the inexperienced 20-something husband: You may want to wear a hard hat the first time you mention that improvement/redesign work is less important than repairs.)
It's important to have clear priority rules with agreed-upon finish dates for jobs. It will improve and strengthen the partnership because the wife and husband (operations and maintenance) will have a joint backlog and joint priorities that can be matched to available resources.
It's important that the husband (maintenance) commit to finish the jobs by the agreed-upon date and that the wife (operations) allow full access to the work area at the agreed-upon time. Both sides must avoid adding on jobs once a project begins.
HANDYMEN AND A PLANIn the plant, it's common to see maintenance personnel managed by operations. These handymen are usually a shift-working resource. If there are many maintenance people on a shift, it usually means that there are plenty of breakdowns or that they work on a bunch of nice-to-have but unnecessary jobs. Either situation is bad, and the root cause (unnecessary jobs and/or poor reliability) must be addressed.
Just yesterday, my wife and I discussed three jobs in the house that "we" feel need to get done. She said she wished that a handyman lived in the basement to finish the jobs at hand. A full-time handyman is, of course, too expensive to keep. The same is probably true for plants. A reliable average-size plant with typical process equipment and, let's say 70 people in maintenance, may have one or two craftspeople on shift for unexpected breakdowns.
Also, maintenance departments have a tendency of not completing work in a timely fashion. This is often due to poor planning and scheduling procedures. When a job is started at home on Saturday morning, it's often unplanned and unscheduled. The work starts with a trip to Lowes or Home Depot, often followed by additional trips there to buy the needed tools or parts.
When jobs aren't done in a timely fashion, the wife threatens to outsource the job to a contractor. (The same occurs in the plant.) Basic planning is a core reliability enabler. Work always takes longer if it is unplanned.
OH, THAT TEENAGERWho is engineering, you ask? It's the teenage son/daughter that you hardly ever see because the kid is locked up in his/her room. You ask the teen to do something over and over and it rarely gets done. In many plants, the engineering department is called "the black hole" because everything you send in is immediately crushed or disappears, similar to the teenage room.
The root cause of this problem isn't necessarily engineering's fault. It's often due to an unreasonable workload and emphasis on big (capital) projects. As a result, your maintenance projects are put aside.
Most plants have too little interaction between engineering, operations and maintenance. Engineering makes designs without much communication with operations and maintenance. Maintenance tends to install equipment without following a management-of-change process, which should include communication between departments, updating of preventive maintenance tasks, bill of materials, drawings, etc.
Now, who is the mother-in-law? Send suggestions to Idhammar@gmail.com.
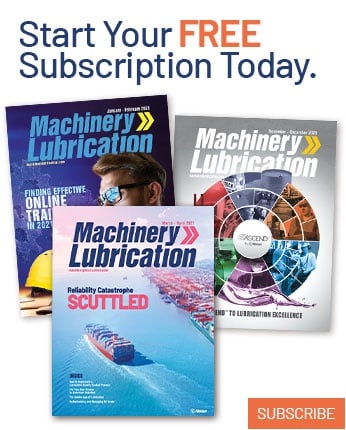