Yuza Yasuda, author of “40 Years, 20 Million Ideas: The Toyota Suggestion System”, describes the spirit of the Toyota suggestion system in this simple thought: “I want to make my work easier to do, even if only a little bit.” He goes on to say, “If people are on the alert to detect problem points, and the environment is created that makes it easy to notice problems, the supply of creative idea ‘seeds’ will not run out.”
Our job as lean leaders is to help create that environment and inspire everyone to act, to take action to make improvements. With Batesville Casket Company’s My CI process, we have seen hundreds of small, simple improvement ideas already implemented to make our jobs easier, even by just a little bit.
A recent My CI idea by a shop-floor associate was to add material stops on the end of a conveyor track. In 20 years of operation of constantly monitoring material on this conveyor and occasionally picking up material from the floor, this “problem” was just considered part of the job. Not anymore, thanks to an alert associate. His supervisor commented that it is amazing that this problem was not “noticed” for so long despite so many people working around it every day.
The opportunities for improvement are truly infinite.
About the author:
Mike Wroblewski started his lean journey with instruction in quick die change from Shigeo Shingo. Mike is currently the lean sensei at Batesville Casket Company in Batesville, Ind. He also writes a blog called “Got Boondoggle?” featuring lean and Six Sigma topics. Check it out at http://gotboondoggle.blogspot.com/.
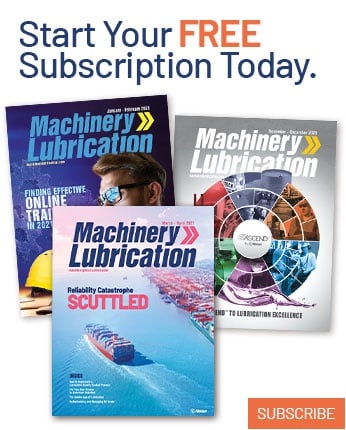