These days, maintenance departments do not need to spend time and money lubricating bearings on the plant floor. Bearing lubrication technology has overtaken traditionally accepted procedures still practiced in many industrial facilities. Self-lubricating plain bearings offer plant-floor decision-makers maintenance-free options to maximize productivity and minimize costs.
There are three types of self-lubricating plain bearings used today. Oil-filled sintered bronze bearings were first conceived in the 1930s, with self-lubricating metal-polymer bearings developed around 1950 and lubrication-free solid polymer bearings appearing in the 1960s. Wear rate and operation under specific loads, temperatures and speeds are all important considerations when selecting the best bearing for your application. The effects of dust, dirt or chemicals on the bearing are also often decisive factors, as well as noise levels and performance alongside different shaft materials.
Figure 1. The benefits of solid polymer bearings include resistance to dirt and impact.
Oil-impregnated, sintered bronze bearings rely on a capillary action to create a lubricating oil film. Benefits include a low coefficient of friction, high precision and rotational speeds up to 1,200 surface feet per minute (sfm). Critically, however, high speed and rotational motion are both required to draw the oil out and maintain a full film of lubricant. Shaft oscillation, slow speed and intermittent use can all inhibit this process. If movement stops, the oil on the surface of the bearing dries up; this can lead to squeaking and an increase in the coefficient of friction. In addition, high temperatures can break down the oil. Further disadvantages with this type of bearing include low chemical resistance and sensitivity to dirt, edge pressure and impacts.
Metal-polymer solutions consist of a metal backing and a thin polymer (such as PTFE) liner. This plastic liner contains a solid lubricant which is displaced from the bearing onto the shaft during movement. The advantages conferred by this self-lubricating layer include a low coefficient of friction and high load capacity — up to 36,260 pounds per square inch (psi) compared to the 1,450 psi achievable with sintered bronze bearings. The bearings are also suitable for high temperatures. However, they are very sensitive to dirt, susceptible to corrosion and do not readily absorb vibrations. The polymer liner can't withstand high edge loads or oscillating movements and is gradually stripped off.
The third, lubrication-free option is to use injection-molded solid polymer bearings. These bearings are made with a mixture of thermoplastic materials, embedded reinforcing fibers and solid lubricant. The fiber-reinforced materials maintain the bearing's strength and resistance to high forces and edge loads.
Figure 2. This split image compares a bronze and a polymer bearing.
Self-lubricating plastic plain bearings offer technical advantages in comparison to metal or metal-backed bearings. A low wear rate, superior chemical resistance and low noise are a few examples. Solid polymer bearings are also impervious to corrosion and have a high load capacity. They are usually underestimated at high temperatures because they are made from plastic, yet short-term temperatures greater than 572 degrees Fahrenheit and long-term temperatures of 482 F are possible.
The dry-running nature of these bearings means dirt particles do not stick to the surface, but instead deflect off it. For this reason, optimal performance can be maintained even in extremely dirty environments.
After the plain bearing itself, the shaft is the most important parameter for a bearing system. This is because it is in direct contact with the bearing and is affected by relative motion. The shaft surface is critical due to the fact a shaft that is too rough acts like a file and, during movement, separates small particles from the bearing surface. On the other hand, shafts that are too smooth can lead to higher wear because not enough lubricant can be transferred onto the shaft to have an effect. Sintered bronze bearings function best on very hard, expensive precision-ground shafts. In contrast, solid polymer bearings have the ability to run on all types of shafts.
Finally, a predictable wear rate is extremely desirable for maintenance professionals. Users should choose a bearings manufacturer with the ability to accurately calculate bushing lifetime in a specific application based on an extensive tribological test database. Currently, this technology is only available with injection-molded, self-lubricating polymer bearings.
One fork truck application has had the latter integrated into its gearshift lever. The plastic bearings withstand 30-pound loads, oscillating movements, 10 cycles per minute and ambient temperatures up to 170 F. They are quieter and cheaper than sintered bronze alternatives and suffer minimal wear. They are also vibration dampening, easy to install and impervious to dirt.
In another application, a swinging hinge assembly used to support PVC swinging strip doors — used for quick loading bay access — has been using maintenance-free, all-plastic plain bearings since 1998 with no problems. The bearings are resistant to shocks and edge loads. They replaced expensive and corrosion-prone needle bearings and steel washers.
This article was provided by igus Inc., a Rhode Island-based manufacturer of self-
lubricating iglide polymer bearings. To learn more, visit www.igus.com, call 800-521-2747 or e-mail sales@igus.com.
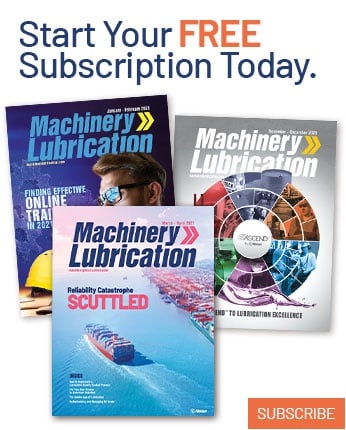