While working this April in Holland, I saw a plant utilizing a marvelous Dutch phrase: "Ja, maar", which means "Yes, but ..." Seeing it first-hand helps me understand a principle of successful planning. Many plants can't implement successful planning because they assign the planners many worthwhile activities that are not planning. "Yes, planning is supposed to really help us, but we need the planner to do this other thing that really helps us." Ja, maar.
What is planning? Planning establishes initial job plans for maintenance work and improves these plans over time using feedback. The craft and time estimates allow scheduling a goal of work for each week matching available crew labor hours. This goal greatly improves productivity. Thus, planning provides a huge boost to crew productivity through helping better coordinate maintenance work.
Figure 1. When utilized correctly, planners improve effectiveness over time.
The caveat, of course, is that a plant can only realize the benefit of planning if it allows planners to plan. Many plants create and staff a planner position and find the planner to be the ideal person to do a variety of activities helpful to maintenance. These activities do indeed help maintenance improve. Yet, they aren't planning activities.
Consider the typical curve of improving maintenance effectiveness with a planner (Figure 1). A plant takes a competent craftsperson out of the workforce to staff a planner position. Area A illustrates the workforce losing overall effectiveness because it has lost a resource. Yet, the new planner soon develops considerable skill in utilizing the plant's CMMS, purchasing bureaucracy and inventory system. Mechanics on the crews leverage the planner's ability to find information and help them more quickly resolve problems for jobs they already have in progress. Yet, this workforce improvement can only go so high, as Area C shows. Furthermore, using planners to help resolve problems for in-progress jobs is not even planning. I call the principal activity of planners in this area "Chasing Parts" because they typically help craftspersons find and procure spare parts not identified in advance on a job plan. Many of those in-progress problems aren't even new. They are reoccurrences of typical problems encountered on those particular machines. This leads to the need for planning.
By considering past maintenance activities on particular machines, planners can plan to avoid specific problems previously encountered - but only if they are allowed time to plan. It takes time to file job feedback and improve job plans. It takes time to figure out plans for work not yet begun. If planners can plan, they can take the organization to levels of effectiveness indicated by Area E. I call this area "Planning Future Work" because the primary duty of the planner should be to head off problems, not help resolve them as they occur.
My main intent in this article is to shed some light on Area B. The chasing parts activity is worthwhile. It does help accomplish work more effectively. We do need to resolve problems as they occur on jobs in progress. Other activities that management might assign planners also help improve maintenance effectiveness. These might include substituting for supervisors on vacation, participating on root cause teams, researching ideas for new equipment modifications, supervising contractors or even writing follow-up work requests from PM inspections. Yet, they sidetrack good planning.
This is why planning has a hard time getting off the ground. When planners try to plan future work, they have no time. "Ja, maar" strikes. "Yes, but" the other activities are important. Area D even shows an initial dip in overall effectiveness if the planners were to stop chasing parts to concentrate on planning future work.
Management must decide if it wants to do planning or not. If other activities are important, assign other resources to accomplish them, not the planners. A plant can't achieve the higher levels of performance without planners planning.
Doc Palmer is the author of the “Maintenance Planning and Scheduling Handbook.” He is a CMRP and has nearly 25 years of industrial experience as a practitioner within the maintenance department of a major electric utility. From 1990 through 1994, he was responsible for overhauling the existing maintenance planning organization. The resulting success played a role in expanding planning to all crafts and stations owned and operated by the utility.
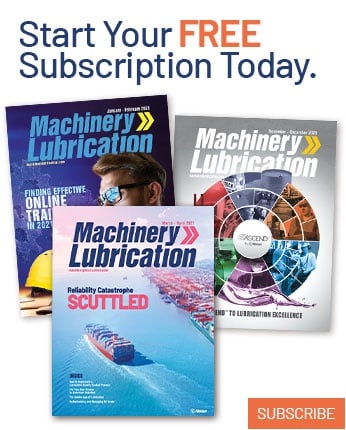