Tom Taranto, a compressed air energy expert with the U.S. Department of Energy, offers you the answers to some common questions he has encountered during energy assessments on compressed air systems. DOE energy experts are skilled at helping industrial facilities identify ways to improve system efficiency.
Question: What benchmarks can I use to check my compressed air system efficiency?
Answer: Compressed air systems and the industries they serve are very diverse. As a result, statistical data necessary to establish industry benchmarks are not available. There are, however, two important measures of compressed air system efficiency; the total air demand of the system, and the compressed air supply efficiency (CASE).
Air demand can be measured in million standard cubic feet (MMscf) consumed over some period of time, for example, daily, such as MMscf/day. According to Compressed Air Challenge Fundamentals of Compressed Air Systems training, 50 percent or more of the compressed air supplied to a typical air system is wasted. It is important to eliminate waste, including leakage, artificial demand and inappropriate use of compressed air.
One measure of compressed air supply efficiency is the CASE Index, determined by metering energy (kilowatt-hours, or kWh) entering, and measuring compressed air flow (in standard cubic feet per minute, or scfm) leaving the compressed air plant. CASE Index is measured as standard cubic feet (scf) per unit of energy (kWh). It has a potential range from zero to 325; higher indices represent better efficiencies.
Another measure of supply efficiency is specific power (kW/100 cubic feet per minute, or cfm), as listed on Compressed Air and Gas Institute (CAGI) standard performance reporting data sheets for air compressors and dryers. See these data sheets in Appendix C of Improving Compressed Air System Efficiency: A Sourcebook for Industry (PDF 1.1 MB). Download Adobe Reader. Equipment efficiency, operating in test lab conditions, is reported as "Specific Package Input Power" and may range from 16 to 24 kW/100 cfm (lower specific power represents better efficiency).
The actual plant air system energy efficiency is affected by many factors, including part-load efficiency, control strategy and the system's supply/demand balance. Increased system efficiency will result in your plant air system's performance more closely approaching the specific package input power of your equipment.
Learn more:
- Compressed Air Tip Sheet #3: Minimize Compressed Air Leaks (PDF 265 KB) Download Adobe Reader.
- Compressed Air Tip Sheet #4: Analyzing Your Compressed Air System (PDF 243 KB)
- Compressed Air Tip Sheet #7: Compressed Air Systems Control Strategies (PDF 243 KB)
Answer: Compressed air power is essential to the operation of most industrial manufacturing and process facilities. However, compressed air as an energy source is extremely inefficient. For many compressed air uses, there are alternatives in equipment or methods that use a more efficient energy source. If the alternative can accomplish the manufacturing task, it may be inappropriate to use compressed air. On the other hand, careful consideration of other factors such as reliability and maintenance may determine that while it is less efficient, compressed air use is still the best choice.
More than 85 percent of the electrical energy input to an air compressor is lost to waste heat. That leaves less than 15 percent of the electrical energy consumed to be converted to pneumatic compressed air energy. For the typical plant air system operating at 100 pounds per square inch gauge (psig), 7.5 horsepower (hp) is consumed by the air compressor to deliver 1 hp of work to the manufacturing process.
One example of inappropriate use that is frequently found is a blowing application that uses compressed air to cool, clean or dry surfaces. Application of low-pressure blowers or fans can often accomplish the blowing task with significant energy savings. High-pressure compressed air is often used for sparging, or agitating a tank of liquid by blowing bubbles through the liquid. Again, low-pressure blowers can be a more efficient energy source. Tank unloading involves pressurizing a tank truck or rail car with air to force the liquid out of the tank. For many liquid tanks, it is recommended that the air pressure be regulated to 18 psig maximum with a safety relief valve set at 20 psig to protect the tank. If air padding is the preferred method to unload the tank, positive displacement-type blowers can provide the necessary air flow and pressure. The use of an electrically driven pump should also be considered.
Learn more:- Compressed Air Tip Sheet #2: Eliminate Inappropriate Uses of Compressed Air (PDF 262 KB) Download Adobe Reader.
- Compressed Air Tip Sheet #11: Alternative Strategies for Low-Pressure End Uses (PDF 247 KB)
This article was published in the U.S. Department of Energy’s Energy Matters newsletter.
About Tom Taranto:
Tom Taranto is an independent compressed air system professional with more than 30 years of experience providing services to industrial clients, utilities and energy agencies. He is the owner of Data Power Services LLC. In addition, he is a DOE compressed air energy expert, senior instructor for Qualified AIRMaster+ Specialists, and instructor for Compressed Air Challenge Fundamentals and Advanced courses. Tom holds a bachelors degree in mechanical engineering from Clarkson University. Contact him at TomTar@aol.com.
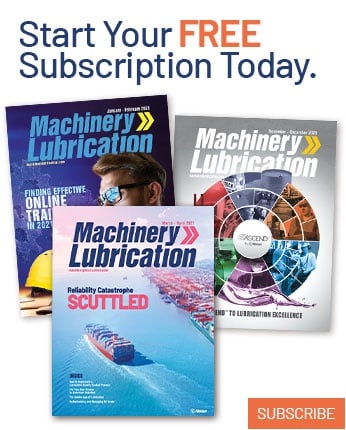