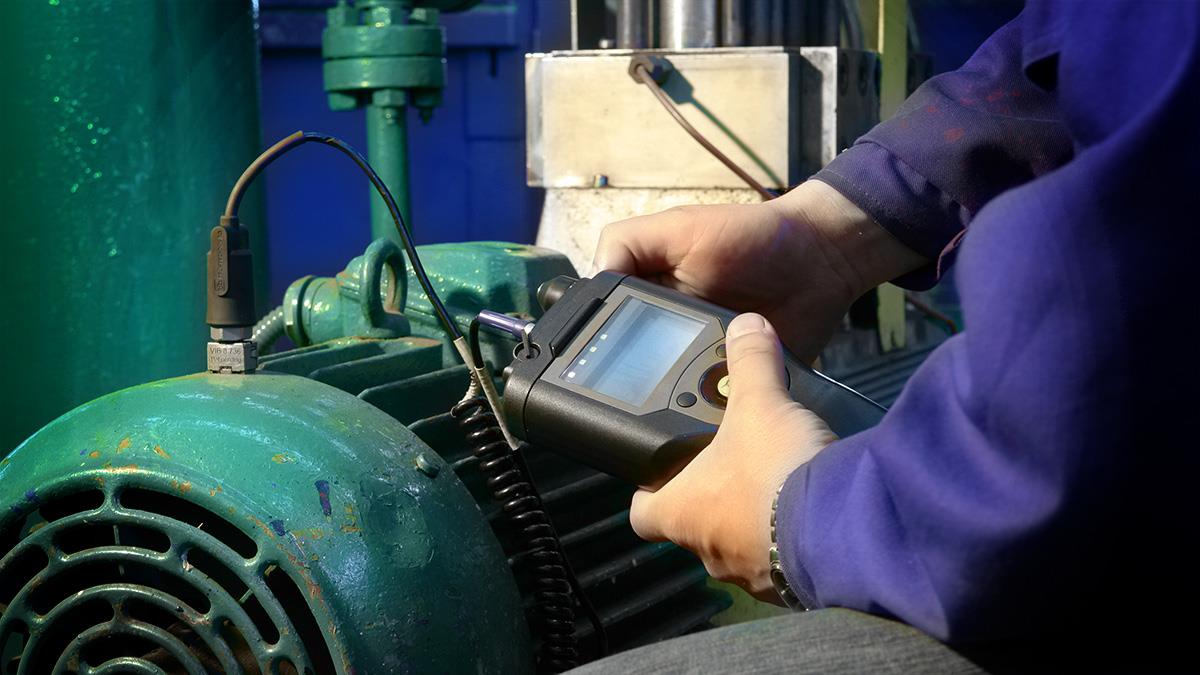
People often think about machine vibration monitoring in one of two ways:
-
A machine is being monitored to avoid catastrophic failure.
-
A machine has a problem, and technicians are employing vibration technology to figure out what it is.
What is often overlooked is how vibration monitoring can help improve planning and scheduling in a way that also reduces maintenance costs and increases production.
Oftentimes, the benefits of Condition-Based Maintenance (CBM) are calculated in terms of catastrophic failure avoidance.
If you detect a defect and shut the machine down before it fails, it results in numerous benefits. When machines fail unexpectedly, they can result in:
-
Secondary damage to the machine or other nearby equipment.
-
Accidents or injuries.
-
Environmental damage in the form of spills or toxic releases.
-
Production losses.
-
Uncertainty in our ability to meet production goals.
-
Adverse effects on our insurance coverage and rates.
-
Lawsuits, fines, and regulatory issues.
Did You Know?
Condition-Based Maintenance can reduce maintenance costs by 25% and eliminate up to 70% of breakdowns.
Source:
IBM
If you already know a machine has a problem, and you use vibration analysis to determine what the problem is, it’s considered reactive maintenance. In this case, a repair is often done soon after the defect is encountered.
When you use vibration analysis as part of a CBM strategy, the goal is to detect defects in advance to gain the benefits of better planning and scheduling.
An important Key Performance Indicator (KPI) is the ratio of planned to unplanned work. This helps you to understand if you are operating the plant in a reactive mode or not; the goal is to have most of your work planned.
The Benefits of Better Planning and Scheduling
There are many advantages that come with deploying vibration analysis to develop an effective planning and scheduling strategy, including:
-
Effective spare parts management.
-
Better deployment of labor.
-
Increased productivity.
Effective Spare Parts Management
If you are confident that you can determine that a part will need replacing months in advance, you do not have to have the spare part in stores. Having your facility keep spare parts in stores has several associated circumstances that can create negative consequences.
For example, parts in stores:
-
Require an upfront purchase, meaning that money cannot be allocated for anything else should the need arise.
-
Require physical space to be stored, which can be a costly expense, especially if a climate-controlled environment is necessary for proper storage and contamination prevention.
-
Must be managed and maintained, which requires technician time and facility dollars to carry out.
-
Have shelf lives. Just because a motor hasn’t been used doesn’t mean it will work properly if it has been sitting in a storeroom for an extended period of time.
Better Deployment of Labor
If the majority of your work is scheduled, you can make more effective decisions concerning your labor deployment.
For instance, you can:
-
Focus facility maintenance activities on the equipment that actually requires repairing. This allows for more effective use of valuable resources.
-
Have a better understanding of your staffing needs, meaning you won’t be under or overstaffed. This saves money and avoids the misuse of technician time.
-
Use your team of technicians more efficiently and increase wrench time. If repair work is scheduled weeks or months in advance, each work site can be kitted with the required spare parts, instructions, tools, and permits. This allows workers to go from site to site and perform the work they need to do in a timely and effective manner without having them wait around for the materials they need to complete their work.
-
Have a better understanding of the skillsets that should be required of your technicians. This also provides you with the time to contract out a specialist for help if necessary.
-
Improve worker morale. Most technicians prefer a well-scheduled week, not a reactive maintenance cycle.
-
Avoid secondary damage to machines, which decreases costs, wastes fewer parts, and extends overall equipment life.
Increased Productivity
If you know the condition of your equipment, you can better manage risk and increase your overall productivity by:
-
Scheduling repairs months in advance of machine or component failure, which minimizes production delays.
-
Taking advantage of unplanned outages to fix other machines that are developing problems.
-
Measuring production levels in terms of Overall Equipment Effectiveness (OEE) and relating these results to the facility’s profitability. A quality CBM program should have a significant effect on OEE and provide a large Return on Investment (ROI).
Conclusion
Overall, Condition-Based Maintenance helps organizations reduce maintenance costs, increase equipment reliability and uptime, and optimize their maintenance resources by avoiding catastrophic failures.
But we must be careful not to use CBM tools and technologies in a reactive mode – if you are finding and resolving equipment problems within days of failure, then you are supporting a reactive cycle and not experiencing the additional benefits of improved planning and scheduling.